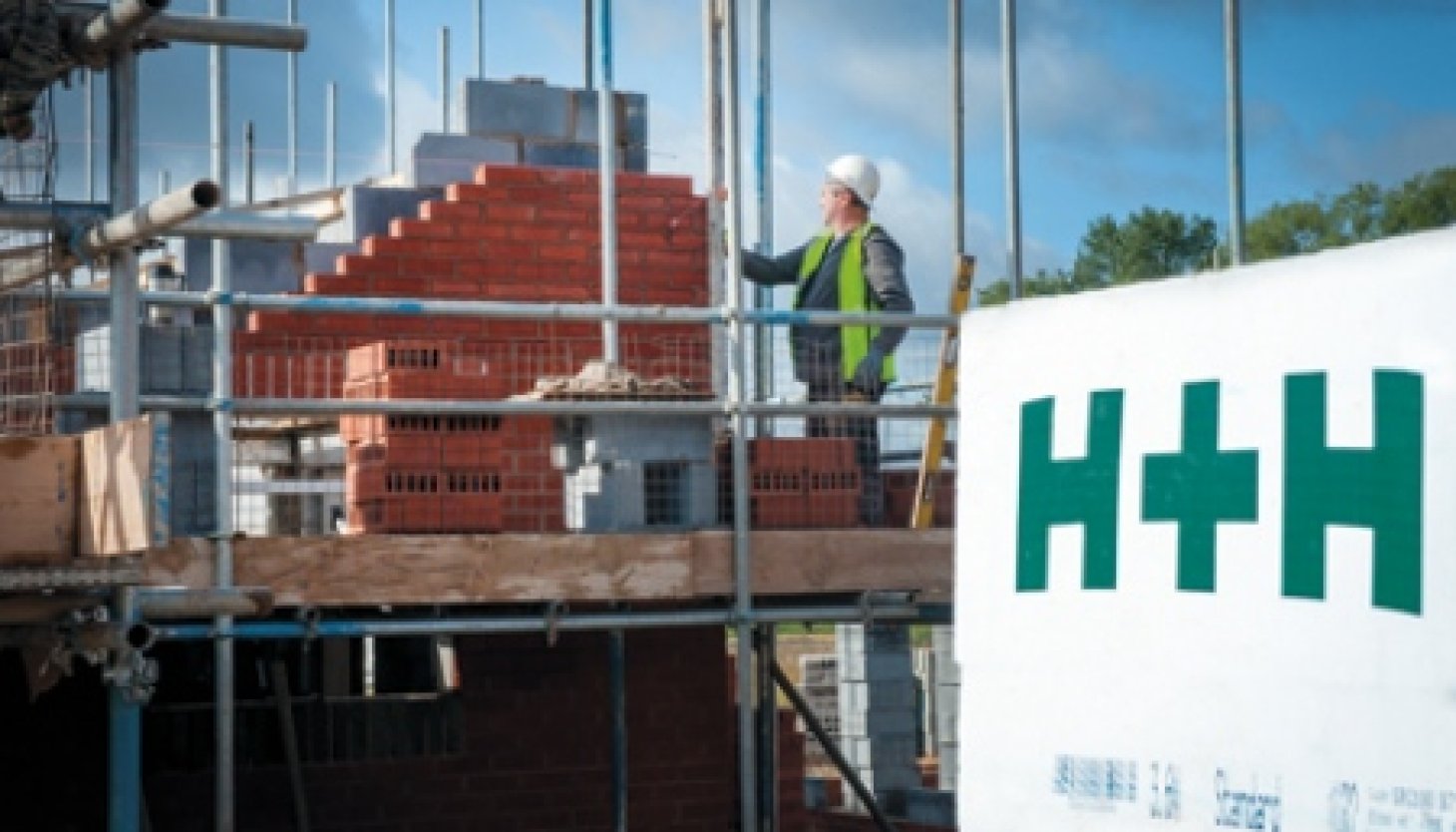
With an enormous multi-purpose residential project to complete, contractor AC Lloyd in Warwickshire reduced costs and simplified logistics by continuing their decade-long collaboration with H+H.
The Oakley Grove project in Harbury Lane at Bishop’s Tachbrook comprises of various designs for 90 properties in the private and social housing sectors.
AC Lloyd, based in Leamington, has a proud heritage of providing high quality homes in both the private and affordable housing sectors in Warwickshire for nearly 70 years.
From their vast experience, AC Lloyd was fully aware that aircrete can provide a building project with greater cost effectiveness and faster build speeds than more traditional materials such as dense aggregate, and the degree of support and assistance afforded to contractors provided by H+H was another decisive factor in choosing aircrete.
The lightweight nature of aircrete leads to a number of functional and financial advantages when compared to more traditional building material; aircrete is actually less than half the weight of the equivalent dense aggregate block.
Dave Henley, Contract Manager at AC Lloyd, said: “We have used H+H aircrete for over 10 years now because its properties help us to consistently produce the fantastic projects that our clients expect from us.
“The light weight of the blocks has a knock-on in all other aspects of the job. They are easy to transport due to the weight, and the lack of weight also allowed our designs to be used with wider spans in beam and block floors.”
H+H prides itself in working closely with contractors and customers to provide outstanding before-sale and after-sale service when they are required. This often includes providing access to the H+H technical team, who are happy to offer guidance on how to get the most out of the system, and co-ordinating closely with orders of aircrete to suit the needs of contractors on-site.
With over a decade’s experience in working with H+H, the AC Lloyd team knew that they could rely on H+H to cater for their specific needs to help in delivering the project to meet their deadlines.
In the Oakley Grove development, AC Lloyd chose to co-ordinate deliveries of aircrete to coincide with progress on the entire project. By taking this approach, H+H helped AC Lloyd ease some of the logistical pressures on the project to save time and money.
Safety was at the core of the decision to use H+H aircrete and all H+H products are rigorously tested before they make their way on to site, providing increased peace of mind to contractors relying on the blocks to perform safely in the long-term. The H+H Quality Assurance System means that blocks are frequently tested and all Grades of Celcon Blocks qualify for category 1 “Manufacturing Control” classification to BS EN 771-4.
Enhanced safety credentials have an all-encompassing benefit on a project. Liberated by the greater confidence afforded by H+H aircrete, designers could reduce the level of safety for their design in accordance with the British Standard.
Fire safety is another important advantage that aircrete blocks possess compared to traditional materials. A 100mm aircrete block from H+H offers fire resistance up to four hours in non-loadbearing situations and two hours in loadbearing situations.
AC Lloyd has made a strong start to the Oakley Grove project, with over 50 homes now completed on time and within budget. The project remains on course for its expected completion in the summer of 2018.To achieve this, H+H assisted the AC Lloyd team every step of the way.