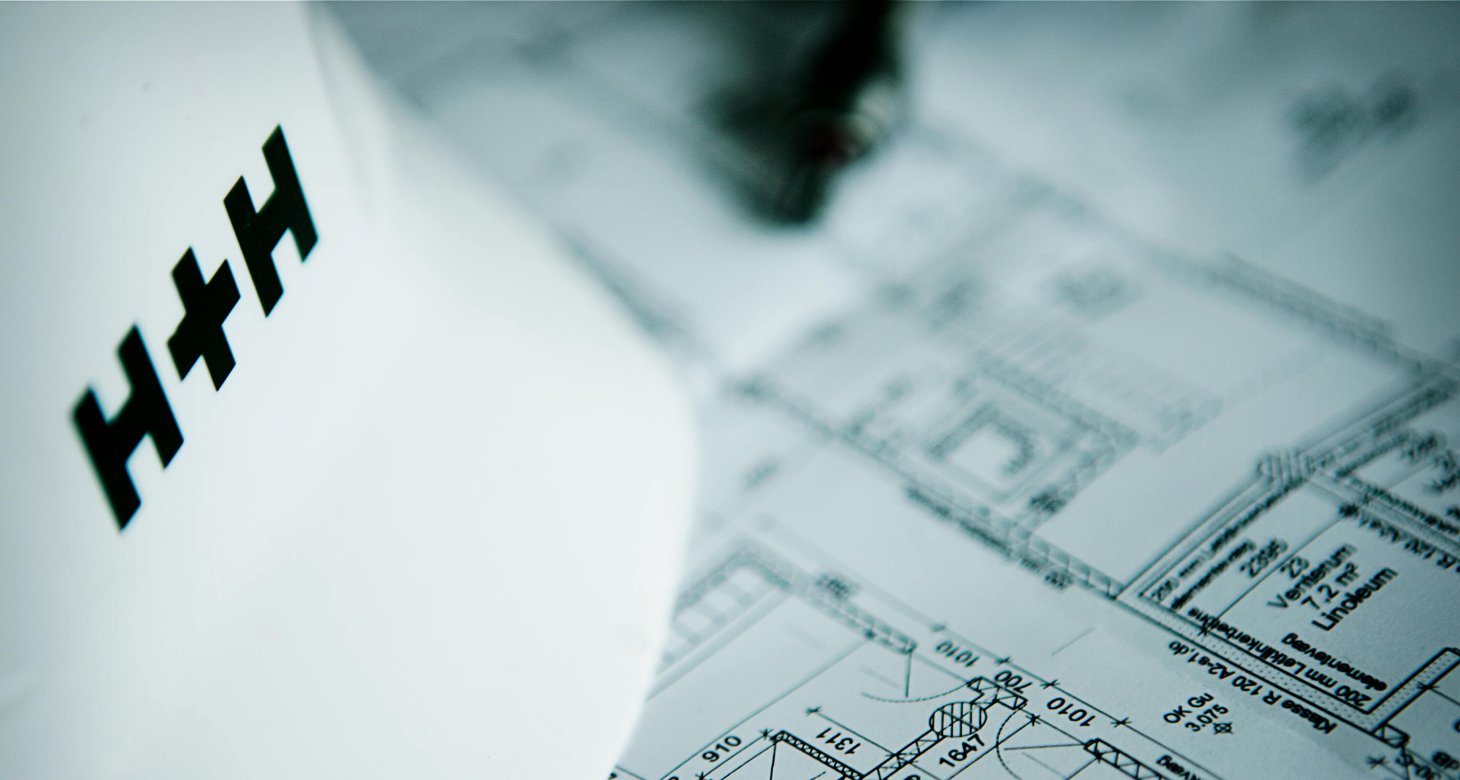
We are all familiar now with the arguments surrounding the need to reduce our carbon emissions. The building industry has responded impressively and new building techniques, as well as new materials, mean that it is quite possible to build houses that have almost no carbon emissions related to their heating needs.
As these techniques become more mainstream, however, the argument shifts. Attention so far has been focused on the carbon emissions in running a building, but in order to produce a general reduction in carbon emissions we must also focus on how much carbon is used to build that structure in the first place.
This argument is beginning to enter the specification world, with more scrutiny now on the embodied carbon of different building materials. I would even hazard a guess that if Building Regulations continue their remorseless focus on the reduction of carbon emissions, future versions may well include limits on embodied carbon figures.
Industry is again responding, with many manufacturers now able to supply accurately calculated figures for embodied carbon – usually described in terms of the carbon required to source and manufacture the products. Whilst there is still a lot of debate about consistent and standard methods to measure embodied carbon, it gives a good starting point. However in isolation embodied CO2 is a meaningless figure. It must first be related to how much of the product is used in the building, so CO2 per m2 of floor area or wall area is more relevant than CO2 per tonne or per m3 of product. Secondly it must be related to service life.
There seems little point in establishing the lowest embodied carbon to complete the initial construction unless the lifespan of the building is also taken into consideration, yet anticipated lifespan is one area that is curiously omitted from most discussion.
This is particularly odd in the area of housing design. A quick look around the housing stock of this country demonstrates just how long we expect our houses to last and yet nowhere is there any regulatory or even official guidance on the issue.
A recent study by the NHBC Foundation began to consider the lifespan argument. The point of the study was to compare operational and embodied CO2 in different types of new build housing. To do so, the Foundation looked at the figures over a 60 year and a 120 year lifespan. Clearly these different figures will give very different results for the impact of the embodied carbon (although I note that nowhere is there any evidence to suggest that all of the fabric solutions under consideration would actually last for 120 years).
As manufacturers we are starting to consider the impact of these types of discussions. One possible outcome could be a demand for all manufacturers to give a figure for embodied carbon that takes account the anticipated lifespan of the product.
In which case, the figure for a product used to build walls would be expressed as an amount of CO2 per square metre per year. This would give a much more meaningful way for specifiers to compare the realistic embodied carbon of the products they choose.
As a society we will be called upon to make choices in the Carbon emissions debate. Is it better to use more carbon now to create buildings that will last for a century or more (which will therefore have a very low embodied carbon per year of life) or better to construct buildings with very low initial embodied carbon but that we intend to last only 25 years?
Personally I think there may be different answers depending on the building type under consideration. There may be an argument that commercial buildings could simply be outdated in fifty years as working practices change and that therefore we should anticipate a regular replacement cycle.
However, in terms of housing I cannot see that this argument would hold true. We have a growing population who need to be housed and the way that we use our houses does not fundamentally change from generation to generation. It takes significant resources to build new houses so it seems most logical to me that they should be built with the intention of lasting for over a hundred years.
If we are to meet our carbon reduction targets then the new homes we build should require minimum carbon to run but we also need to consider the carbon emissions in building them.
Investing now in robust, durable structures will prove the most efficient use of resource over the longer period.
If I am right, and this is the direction that regulatory bodies move over the next few years, then we should expect to see all manufacturers being as outspoken about the embodied carbon of their products per square metre per year of service life as they are currently about their U-value.
This article originally appeared in BMj magazine, February 2013