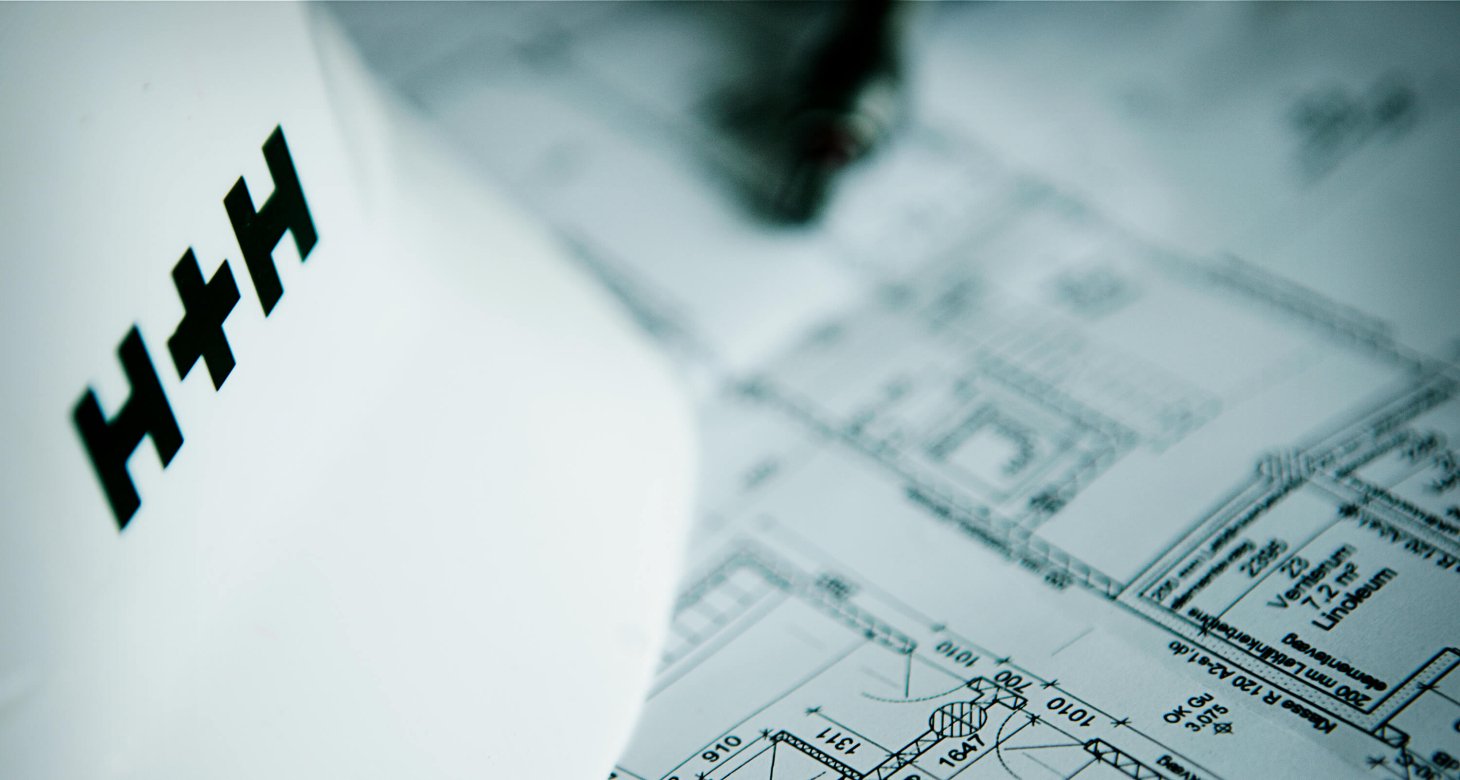
In March of this year the Office for National Statistics (ONS) announced that the rate of inflation faced by households in the UK had fallen to 1.6 per cent in the year leading up to March 2014.
This was the lowest rate since October 2009. It has since increased to 1.9 per cent but this is still below the Bank of England’s target rate of two per cent and significantly less than the 5.2 per cent rate we faced in September 2008. This provides George Osborne the ammunition to declare that the Government’s economic strategy is working.
Whilst low inflation is welcome news for consumers, it is a very different story for the long-term sustainability of the building industry supply chain.
The Story of Supply and Demand
From 2008 up until last year, the supply of building products and materials exceeded demand and competition between manufacturers has been fierce. Rivalry for sales volumes drove down prices to unsustainable levels, cutting into margins that are necessary for re-investment. Many manufacturers were forced to take drastic action simply to remain competitive and in business. At H+H this meant closing an entire factory and making a lot of people redundant.
Prices of building materials have remained low to builders but we now have five years’ worth of pent up inflation. The prices of some products are as low as they were in 2007 despite very large increases in manufacturing and energy costs over the same period.
With supply and demand more evenly balanced, manufacturers will be looking to rebuild margins to more sustainable levels. As an industry we have lost a number of manufacturers in the depression and to lose any more would certainly have a negative impact on the entire building industry. It is vital that manufacturers are able to invest in their facilities; firstly to deal with the backlog of under-investment during the dark years and secondly, should the current recovery prove to be sustainable, to build back capacity that will allow for a continual increase in manufacturing output to keep up with demand.
Current State of Play
For the first time in five years, many building materials manufacturers throughout the country are increasing their prices and merchants are passing these on to builders. I can understand why builders may not welcome these price increases.
Many companies are busier than they have been for years; consequently putting pressure on labour rates and some are struggling to get hold of enough tradespeople. However, at the same time house builders are reporting very healthy profit increases. So, they should be in a better position to share some value with the rest of the supply chain; in the same way as the supply chain responded with cost savings in the downturn when house builder profits disappeared.
The Alternative
The alternative to prices rising to levels that encourage British manufacturers to invest is for builders to increase their reliance on imported materials. The problem with relying on imports is that, unlike many other commodities, the cost of imported building materials is usually higher than locally sourced products. This is particularly the case for the heavier products due to the cost of transporting and shipping.
Importing more products also flies in the face of the Government’s Industrial Strategy for Construction goal of a 50 per cent reduction in the building materials trade deficit by 2020. Importing also worsens our carbon footprint and makes our economic recovery unbalanced and more dependent on the services sector.
Whilst UK GDP recently exceeded its pre-recession peak, manufacturing remains eight per cent below and 30 to 40 per cent of building materials used on UK construction sites are imported. A lopsided economic recovery is likely to be less sustainable which in turn could have consequences for the house building recovery too.
Future Requirements
House prices are frequently used to bench mark the strength of the home building industry.
In the past year the average house price has gone increased by over 9 per cent to over £250,000. But excluding the land value and the cost of meeting planning conditions in terms of roads, school buildings etc.., the cost of building an average home is around £60,000 of which materials account for less than 50 per cent.
Looking at the price of materials with that in mind, a 10 to 20 per cent increase, which is approximately the level that prices need to rise by, would be less than one quarter of the value that house prices have risen over the past year.
Building material prices will continue to increase at a faster rate than inflation until manufacturers’ margins recover to levels that sustain investment. If they do not, getting investment in the UK could be quite a challenge. The reason for this is that the majority of UK building products and materials companies are subsidiaries of global, foreign owned companies that have a choice of where to invest. Of the 21 manufacturing members of the Construction Products Association (representing the largest building material suppliers in the UK) just two are UK owned, compared with 20 years ago when just two were foreign owned. Investments in the UK are competing for capital with opportunities in, for example, Brazil and Indonesia which are faster-growing markets and possibly more sustainable too.
This is very important because if we do ever get to building over 200,000 homes per annum in England, which seems to be the ubiquitous target of politicians of all colours, the only way to be certain that we can meet the demand for materials is to keep investing in our manufacturing infrastructure.