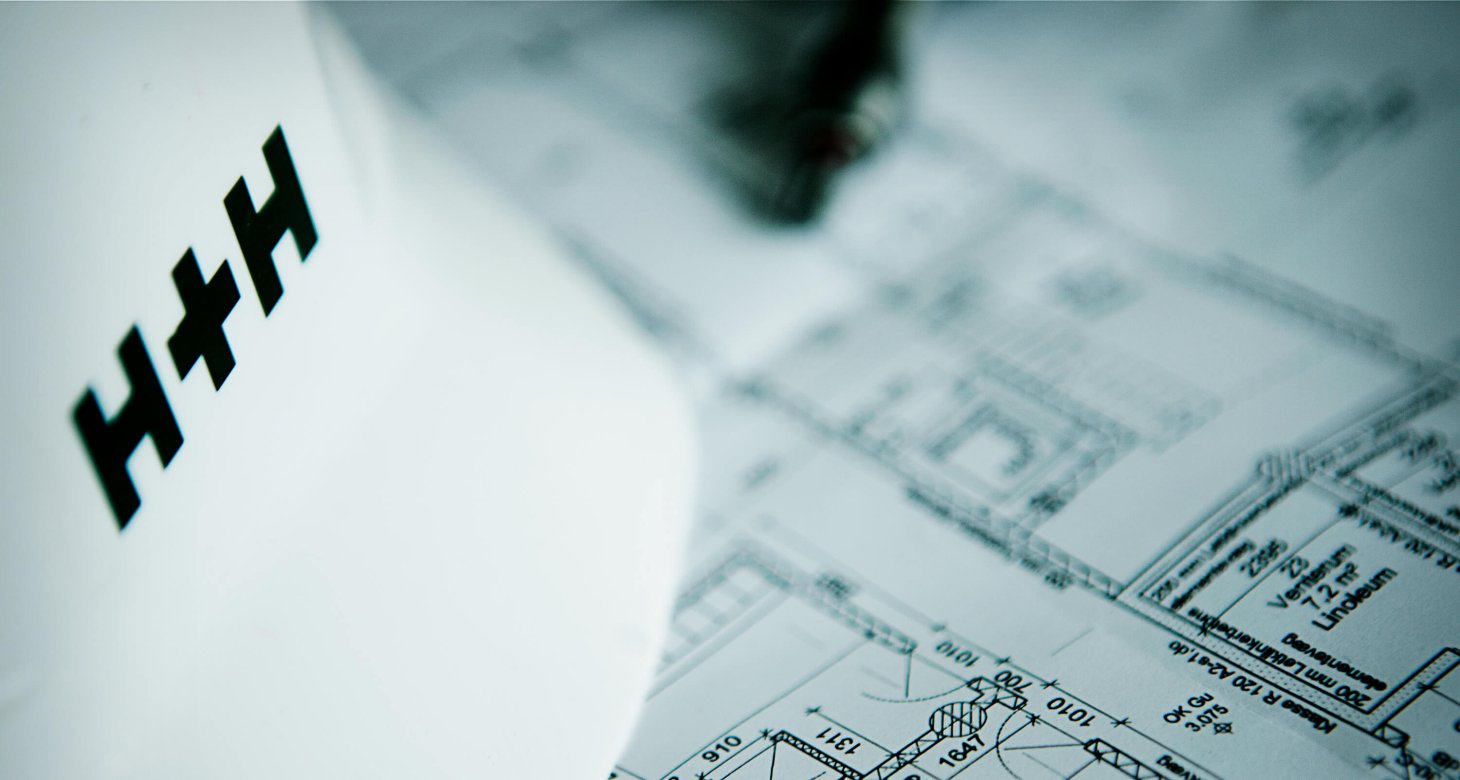
Demand for building materials has exploded over the summer. Why? Is this permanent? And how are manufacturers responding to the challenge? Mark Oliver, MD of aircrete block manufacturer H+H looks at some causes and solutions.
What a difference a few months can make! We entered 2013 feeling relatively optimistic, anticipating a modest rise in demand fueled by a predicted increase in new housing starts of about 3%.
The first quarter of 2013 was disappointing in sales terms and a decline on last year. Bad weather affected sites, the economic outlook was improving but very slowly.
And then came the budget with the Help to Buy initiative. New mortgage applications were actually on the rise before then, but there is no doubt that Help to Buy has really shaken up the new build market.
As late as April this year many forecasters (such as CPA, Experian etc) were predicting that the rise in new housing starts in 2013 would be between 2.5% and 8%. Despite a disappointing first quarter, we at H+H decided that conditions were set to improve and started gearing up by adding extra shifts at our production plants and building stocks.
Even with our own optimistic view of the market we could not have anticipated the staggering rise in activity in June and July. We were not alone in seeing, over this short period, products moving faster than at any time in the last ten years. Looking at how different sectors have responded to this dramatic shift is instructive.
Help to Buy is working. The government’s intention was to stimulate the market for new housebuilding and the number of new houses being built is definitely on the rise. The Department for Communities and Local Government has stated that 10,000 applications have been received during the first four months of the scheme and that seems to equate to an additional 10,000 housing starts in the latest forecasts.
In typical British fashion, media reporting of the scheme has chosen to focus on potential risks of the scheme overheating rather than to consider that the objective of the programme: to get more houses built, is being achieved.
True, there is a debate about whether the scheme will fuel house price rises and this is a concern, but if you believe, as I do, that the fundamental problem with the housing market is a lack of supply, then the only solution is to generate a larger quantity of new housing.
The next problem for suppliers is how to meet such a dramatic increase in demand. June and July were exceptional months. Although they reflect an increase in new housing starts, there were also additional factors that created a one-off peak that we believe will calm during the third quarter of this year.
What we have seen is customers starting to build stocks again. During the last few years merchants and builders have grown accustomed to being able to order product at extremely short notice, so when, in May, we asked our customers for forward orders not everyone responded. At H+H, we geared our manufacturing to ensure we could meet all of our forward order commitments, but outside of this, supply has been tight.
We have followed our normal policy of honouring our commitments under existing contracts and prioritised existing customers even if that means sacrificing potentially lucrative new deals with organisations desperate for immediate supplies.
Faced with a fear of a shortage of products many customers responded by doubling their usual orders and building their own stocks to hedge against potential future shortages, exacerbating an already tight supply situation in July and August.
A hint of a possible shortage of product will always cause a surge in orders, but there is no reason to believe that there will be any long-term capacity problem in our own product sector.
At the start of this year the aircrete industry in general was working at levels significantly below capacity. We started to increase our speed of production in May and have continued to recruit manufacturing staff. I would assume that our competitors are doing the same, so there is plenty of breathing space for manufacturing to meet demand. The suddenness of the upturn has caused a short-term issue, but it is not a structural problem.
The Construction Products Association (CPA) is currently predicting a 39% growth in new housing over the next three years. If they are right then by then end of 2015 we will still be 20% short of the level of housing starts that achieved in 2007. This level of growth will easily be supported by increased output from manufacturers.
Having seen all manufacturers take steps to bring on more capacity, I am confident that even if the more optimistic predictions for new house building in 2014 are achieved our industry will be able to meet demand. It certainly makes a refreshing change to be focusing on the challenges of how to increase production fast enough!