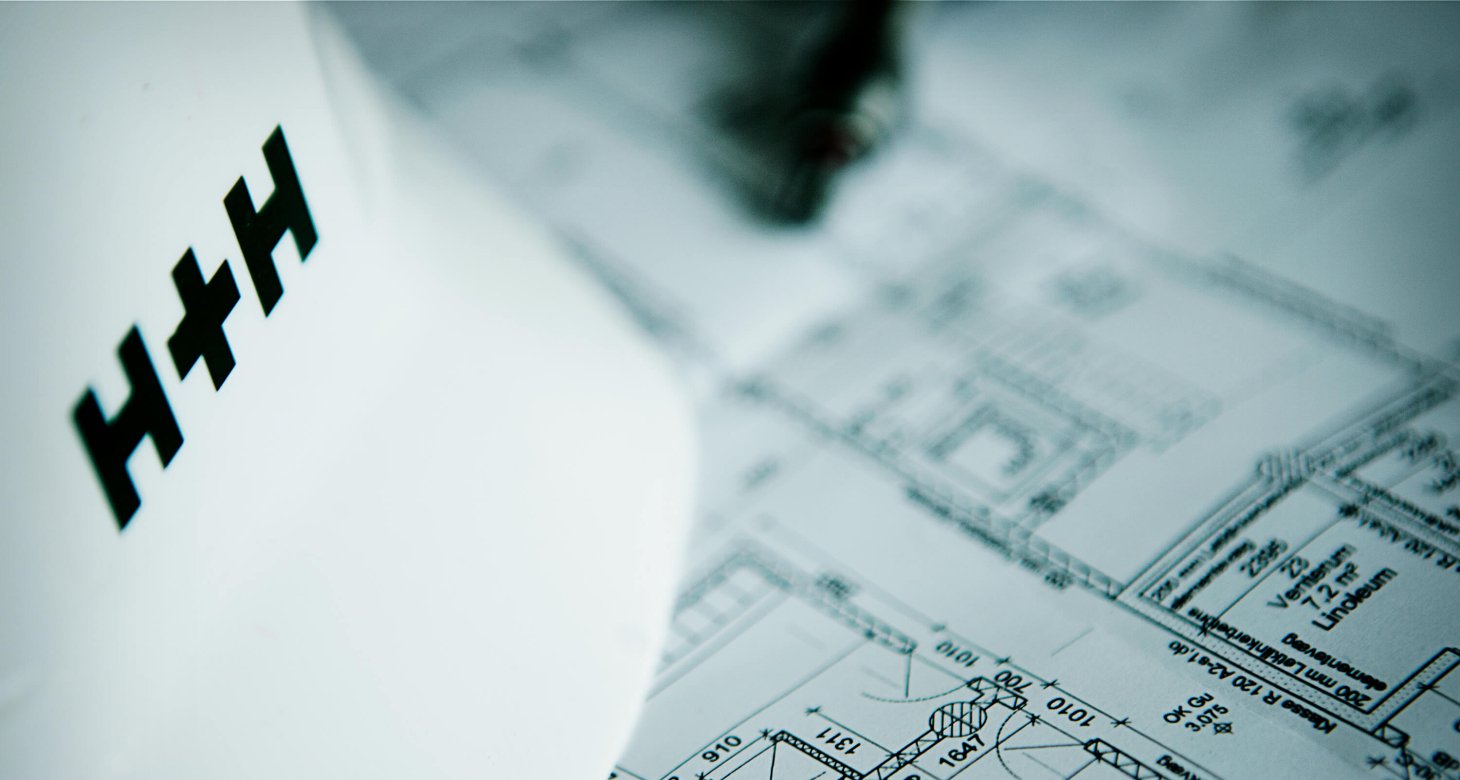
In September 2012 Vince Cable announced that the Government would be developing eleven sector strategies across key industries during 2013 with the aim of promoting both short and long term economic growth. The construction industry was selected as one of the eleven sectors and a Construction Industrial Strategy Advisory Council (CISAC), representing the breadth of the industry, will oversee and steer the development of the strategy out to 2025.
The CISAC is made up of 18 business leaders from the construction supply chain (more details available at BIS.gov.uk). Builders Merchants are represented by Geoff Cooper, Chief Executive of Travis Perkins Plc, and David Pinder, Chief Executive of BDR Thermea, is representing the building product manufacturers.
The industrial strategies are not just driven by the Department for Business Innovation and Skills (BIS) but are a cross Government initiative involving the Cabinet Office. The task of delivering the industrial strategy for construction by the summer of 2013 falls on the new Chief Construction Advisor (CCA), Peter Hansford , who reports to both Michael Fallon the Construction Minister at BIS and Francis Maude the Minister for the Cabinet Office.
Our industry already has something called the Government Construction Strategy (GCS), launched in July 2011, which has the overarching aim of reducing the cost of Government construction projects by 15-20% by the end of the Parliament. The new Industrial Strategy for Construction (ISC), which is to be launched in the summer of 2013, will not supersede the GCS but it will have a much wider remit, although planning policy is one area that is excluded.
The latter is a bit of surprise given that construction is a service industry that delivers infrastructure, housing and buildings. Having a strategy for construction without a strategy for planning our infrastructure or housing is a bit like having a strategy for the nursing “industry” without having a strategy for the NHS. However, Peter Hansford has said that the new strategy will bring together the different strands of work being done, in areas such as low carbon construction, BIM and efficiency and reform, which he said industry often perceived as fragmented.
But I also strongly urge that within this overall construction strategy there is provision for the domestic building materials supply industry because, if current trends continue, it may not be fit for purpose in 2025.
Increasing Imports
Today, the domestic building products and materials sector accounts for around 4.5% of GDP and 15% of all goods manufactured. As the Get Britain Building website states, 92p of every £1 spent on construction is retained in the UK supporting the manufacturing and skill base that we will need for the future.
However, over the past decade, the UK construction industry has increased the amount of building products and materials that it imports with the growth in imports dramatically exceeding the growth in exports. Analysing figures from BIS and the Office of National Statistics (ONS) reveal that this has worsened since the beginning of the financial crisis. In 2008, 34% of building products and materials, by value, used on construction projects in the UK were imported and this increased to 41% in 2011, the year for which the latest statistics are available.
There has also been a dismal record of imports increasingly outstripping exports to the detriment of our own domestic production. The deficit currently stands at over £6 billion per annum, having grown from £2 billion in 2000.
Even imports of heavy side materials which, due to high transport costs, are local rather than global products, have been rising. As an example, data from the Mineral Products Association (MPA) reveals that whilst UK cement sales declined 22% between 2001 and 2011, imports increased threefold and the market share of imported cement grew from 3% to 12%.
Capacity Reduction
During the past five years of economic depression, the UK building materials and products industry has dramatically reduced in size with over 30% of its production capacity closed or mothballed. Around 20% of that capacity has been permanently removed as plants have been scrapped or exported overseas to countries like India.
Using cement again as the example, in 2007 there were 15 operational kiln sites producing cement clinker in the UK but there are only 11 operating today (a 27% reduction). Of the four sites that have closed, one will never produce clinker again as it has been converted to grind imported clinker. The same could happen to the other sites and is also happening with other products and materials.
Along with the capacity reduction we have also seen a significant decline in the number of players and jobs. According to ONS data, there were just over 15,000 companies in the building products and materials sector in 2008 before the recession but this reduced by 10% to below 13,500 in 2011, with a further drop expected when the 2012 figures are released in June.
Competing for Investment
When market demand grows and outstrips the reduced capacity that we now have, there will either need to be investment in new capacity or failing that imports will need to rise further. But getting investment in the UK could be quite a challenge. The reason for this is that the majority of UK building products and materials companies are subsidiaries of global, foreign owned companies and when the time comes to invest say £150m in a new cement plant or £25m in a pre-cast concrete facility, there will be other opportunities in Brazil or Indonesia which will be faster-growing markets and probably more attractive places for these companies to invest.
Of the 21 manufacturing members of the Construction Products Association (representing the largest building material suppliers in the UK) just two are now UK owned, compared with 20 years ago when just two were foreign owned.
Aggregate Industries | ---Swiss, Holcim Group | --
BASF | ---German, BASF SE | --
BDR Thermea | ---Dutch, BDR Thermea Group | --
Caradon | ---US, Honeywell International Inc. | --
CEMEX | ---Mexican, CEMEX S.A.B. de C.V. | --
CRH | ---Irish, CRH PLC | --
Dow Chemical Company | ---US, The Dow Chemical Company | --
Etex | ---Belgian, Etex Group PLC | --
Grafton Group | ---Irish, Grafton Group PLC | --
Hanson | ---German, HeidelbergCement AG | --
Kingspan Group | ---Irish, Kingspan Group PLC | --
Knauf | ---German, Knauf Group | --
Lafarge -Tarmac | ---French, Lafarge S.A | --
Marshalls | ---UK, Marshalls PLC | --
Pilkington | ---Japanese, NSG Group | --
Polypipe | ---UK, Polypipe Ltd. | --
Rockwool | ---Danish, ROCKWOOL International A/S | --
Saint-Gobain | ---French, Saint-Gobain S.A. | --
Tata Steel | ---Indian, Tata Steel Ltd. | --
Wavin | ---Dutch, Wavin Group | --
Worcester Bosch | ---German, Robert Bosch GmbH | --
The UK construction industry won’t go short of materials because the multinationals that serve the UK market will be able to ship products from factories they own in Europe, North Africa or further afield. However, the jobs and economic activity that you would expect to come with increased construction activity will not increase by as much as the construction output. In addition, the benefits of short lead times, just-in-time supply and innovations specific for UK market needs won’t be there to be captured by those who integrate and assemble the solutions.
UK jobs and UK economy
And whilst exporting manufacturing overseas will undoubtedly reduce the UK’s carbon emissions, it will have the opposite effect on global carbon emissions as the products are transported over longer distances and are manufactured in factories that are less efficient and/or more polluting than the ones we had in the UK.
Tilting the Playing Field
As it stands today, there isn’t a level playing field for UK-based manufacturers. The MPA and the Confederation of British Industry (CBI) have highlighted the consequences ofglobally unequal carbon pricing on UK manufacturing and the ‘carbon leakage’ that threatens to increase the rate of manufacturing loss from the UK. A number of other factors make it more difficult to manufacture in the UK, including higher energy prices and taxes on carbon emissions through the CRC Energy Efficiency Scheme.
Many importers, particularly for timber based products, are strongly supported by their respective Governments. The Industrial Strategy for Construction should consider steps to at least level the playing field for UK based manufacturing or, better still, tilt it in our direction. After all, that is what the French and Germans would do…
One of the things I would expect in the Construction Strategy is a vision for the construction industry in 2025. And within that vision for construction, I strongly believe there should be a vision for the building products and materials industry.
My suggestion is that this vision should be that 70% of building products and materials used on UK sites should be sourced from within the UK. So, if you agree with me, please do lobby Geoff Cooper and David Pinder…
This article originally appeared in BMj magazine