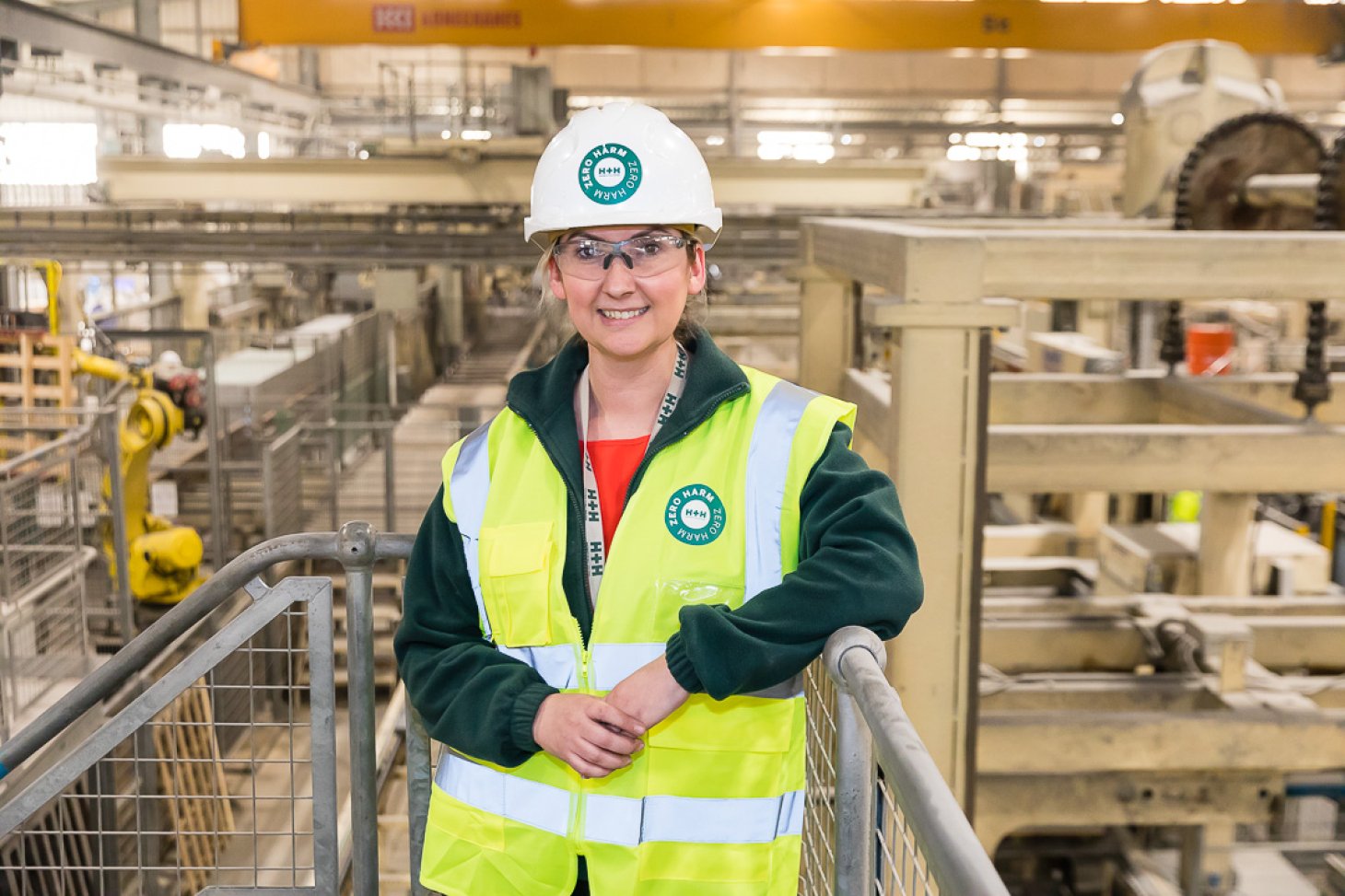
Rachel Rhodes is Production Manager at one of H+H’s plants in Pollington, East Yorkshire. Her job is to ensure the plant meets its output targets, and to manage the training, development and safety of factory workers.
There is a neat symmetry to the course of Rachel’s career path. She joined H+H as a Continuous Improvement Engineer in 2021 where she was responsible for analysing the production process to identify any improvement areas and putting plans into place to resolve them. Her current role is a natural progression of this work although she now has as much responsibility for people as for the manufacturing process.
Rachel’s background in continuous improvement has given her the tools and experience to develop processes to help everything run smoothly. Part of her day-to-day job is the management of raw materials and ‘right first time’ production. She resolves any issues that might affect manufacturing output, that may involve arranging maintenance support or identifying and resolving a resource gap.
Rachel enjoys the variety of the job: “I relish the challenge that comes with every day being different, but while two days are never the same the goal never changes: my focus is on producing high quality product and meeting customer demand.”
Describing herself as a ‘people person’ one of the things Rachel likes most about her role is working with people: “One of my key objectives is to multi-skill operators so they can work on different areas across the factory floor. I love seeing people develop in their roles and watching them progress through the company. I take personal development seriously, both my own and my team’s. I believe that if you want to progress you should always be working on your next steps.”
Rachel has standardised training for site workers to make sure it is consistent and to make it easier for people to do their jobs correctly and safely. Part of this has involved accommodating different training needs in recognition of the fact that people learn differently, including introducing a set of visual tools to help people learn their job. This has been crucial with the recent reopening of the Pollington One plant to ensure new operators are trained effectively.
Introducing new processes brings its own challenges as many people are naturally averse to change. However, Rachel believes the benefits are worth it: “When a change is introduced people often question why we need to do things differently, however when it’s a success and makes their job easier to do, they see the value.”
“I always follow the DMAIC process: define, measure, analyse, improve, control. It’s the way I’ve been trained to get to the root cause of issues or potential issues. I never make assumptions, I use data and follow a methodical approach. This means measuring a starting base point, making improvements, measuring the success of those improvements and tweaking any processes to ensure everything is working at the optimal level. This way of working brings structure and standardisation.”
Rachel knows that success in manufacturing isn’t just about processes, it’s about people. By placing a strong focus on training and development, she’s helping H+H meet today’s production demands while building the skills needed for tomorrow.