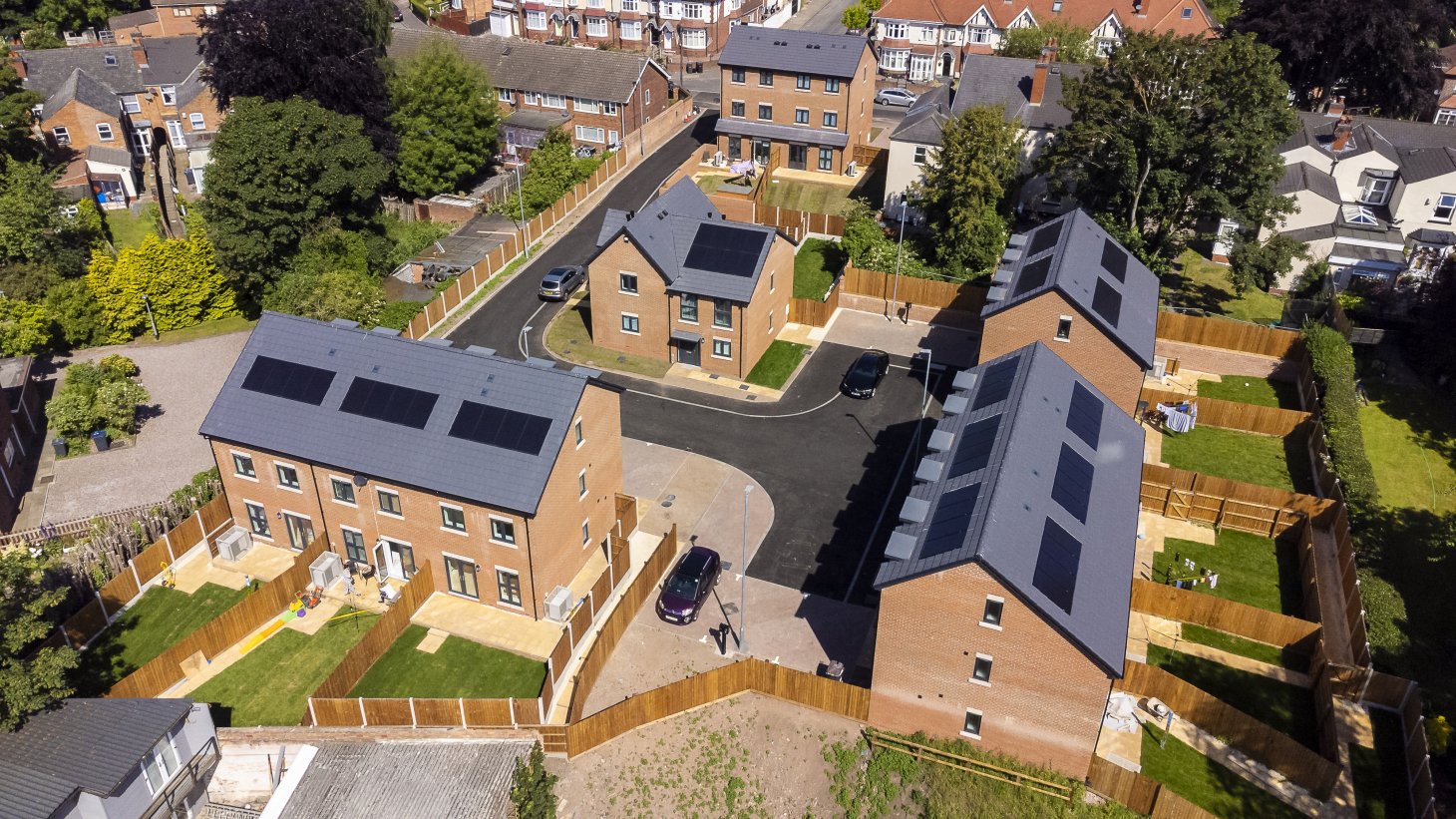
Project 80 is a Future Homes Standard research project from social housing provider Midland Heart in collaboration with Birmingham City University. The project explores the potential for constructing homes that meet the 2025 Future Homes Standard regulations, and initial results published in July show promising indications of substantial carbon reductions.
The first of its kind, Project 80 is a series of housing schemes built by Midland Heart and Tricas Construction. The objective is not just to meet the 2025 Future Homes Standard but to surpass it eventually. The project's inaugural phase saw the successful construction of 12 new homes in Birmingham in May 2022, utilising three distinct combinations of materials and technologies.
For the past year, Birmingham City University has been meticulously researching the project's first development, Eco Drive. The focus is to evaluate the effectiveness of different construction configurations in minimising carbon emissions. Ultimately, this research seeks to inform future decision-making about constructing resilient, energy-efficient social housing on a larger scale.
The recent report analysed three different housing types, with two being built using H+H aircrete and technologies that included heat pumps, photovoltaic panels and mechanical ventilation systems. The homes were designed to achieve 80-90% reduction in carbon from 2013 regulations.
Results were positive showing that when heat pumps and PV panels were combined in a masonry home, a 70% carbon reduction could be achieved over gas-heated homes. Occupants were delighted at the level of comfort in the homes and noted a small reduction in bills.
The data from the project has already provided valuable recommendations for what needs to be done to achieve the 80-90% carbon emissions reductions. These include increasing insulation in walls, enhancing the window specification, increasing the levels of airtightness, educating occupants on effective heating and ventilation strategies and providing advice on how lifestyle impacts a home’s operational carbon emissions.
Evaluating building performance included looking at the building fabric and build quality through airtightness testing and thermal imaging. The design value for thermal bridging heat losses (y-value) at the junctions were 0.028 (lower than the 0.05 indicative value for the Future Homes Standard). Thermal images confirmed that good detail design and execution led to a reduction in thermal bridges and therefore, an increase in indoor thermal comfort.
A key takeaway from this initial study is that good buildable junction details need to be available to assist designers, energy assessors and small- and medium-sized home builders in ensuring air tightness and minimising cold bridging.
This is something that H+H has readily available. We provide junction details, available in CAD or PDF format and over 2,000 compatible calculated thermal bridging values, to assist with the accurate construction of junctions. These resources are useful for anyone building with our aircrete products and can be downloaded from the H+H website for free.
Project 80 is well on the way to providing a more than viable model for building the future homes we need, proving thus far that brick and block construction is undoubtedly part of that future.
Read our introductory blog on Project 80 here.