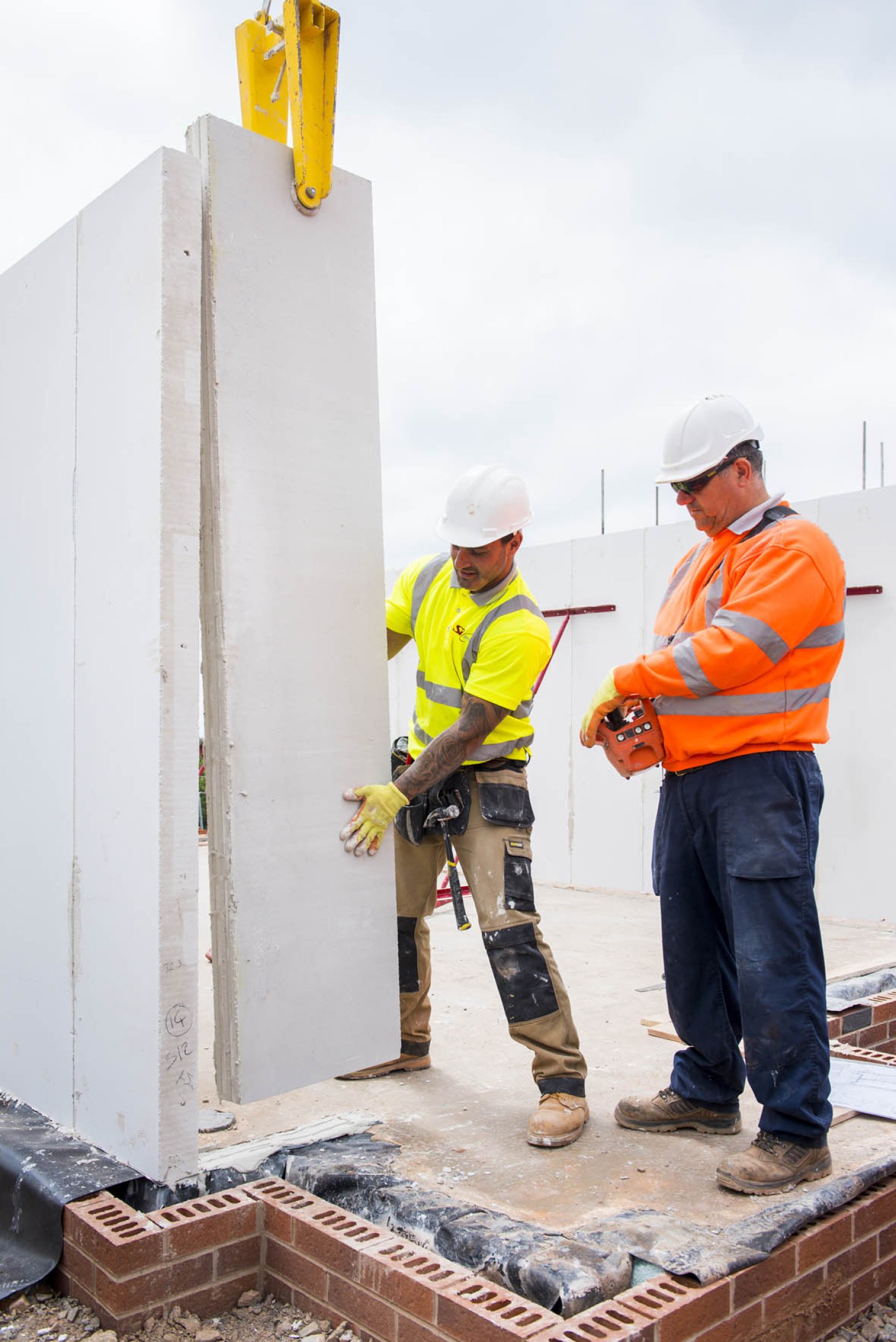
It’s an exciting time to be in the construction industry. The Government has recently unveiled details of its Construction Sector Deal which means record investment for the industry as the country moves in to unchartered waters post Brexit.
A recent report from the House of Lords’ Science and Technology Committee recognised the benefits of off-site manufacturing but warned this method alone can’t meet the demand for Britain’s homes. When giving evidence to the committee, Mace Chief Executive Mark Reynolds explained that off-site is not seen as tried and trusted by the industry, which explains its slow start.
The final report goes in to more detail about the constraints faced by off-site manufacturing and expresses concern about the need for factories and equipment to be provided before any houses can roll off the production line: ‘At present the upfront finance required to set up off-site manufacture appears greater than the finance required for conventional construction’.
From a client’s perspective, off-site manufacture requires long-term commitment, including agreeing to production and timescales well in advance of any unit sales (often several years). Housebuilders, like any business, are understandably wary of making a significant investment without uncertain returns, especially given the current political climate.
If market conditions cool once Britain leaves the European Union, it may be difficult or even impossible for manufacturers of modular housing to adapt quickly and reduce output.
Here at H+H, we believe we have the solution. As the UK’s largest manufacturer of aircrete, we are committed to modern methods of construction (MMC) that provide cost-effective solutions which make use of the industry’s existing skills base. This is what led to our pioneering partnership with SIG Off-Site to create the innovative I-House system.
The SIG I-House System, based on the storey-high aircrete panels, delivers a complete house shell with weathertight roof and wrapped in insulation in just one week. The system is highly adaptable but in all cases, the Celcon Elements are used for the inner leaf of the cavity walls and for the internal partition walls including separating walls.
Where required, standard thin-joint aircrete blocks are used in combination with the Celcon Elements, allowing the system to accommodate non-standard details such as bays. This solves one of the key criticisms of other off-site methods which require designs to be finalised several months before production.
Requiring just a three-man gang to crane into place, the Celcon Elements are fixed using fast-setting element mortar. The ground floor panels are then supported with props to allow prefabricated floor cassettes by SIG to be fitted and for the second-storey panels to be fixed above the floors. The roof consists either of standard truss construction or the ‘Roofspace I-Roof’ panelised roof system. The SIG I-House System also includes all lintels and cavity wall and party wall insulation.
The award-winning system was successfully trialled at Barratt Homes’ 164 unit Norton Farm site in Bromsgrove.
Steve Cartwright, Barratt Construction Director for the West Midlands observed: “It’s simply one of the best offsite systems we’ve seen. It’s basically blockwork erected in a different way which gives us flexibility on site. If you require any design alterations while on site, you can treat it like a traditional build – if you need an additional window suddenly, you can do it, whereas with timber frame you can’t alter this due to the structural calculations changing.”
The Government’s support for off-site manufacturing should be welcomed, however this needs to be balanced with an understanding of the construction industry which is often criticised for being slow to change. Our SIG I-House System combines the speed and efficiency benefits of off-site with the traditional methods the industry is comfortable with. To learn more about the system can be used on your next project, contact the H+H Sales Team today: info.uk@hplush.com or call 01732 886444.