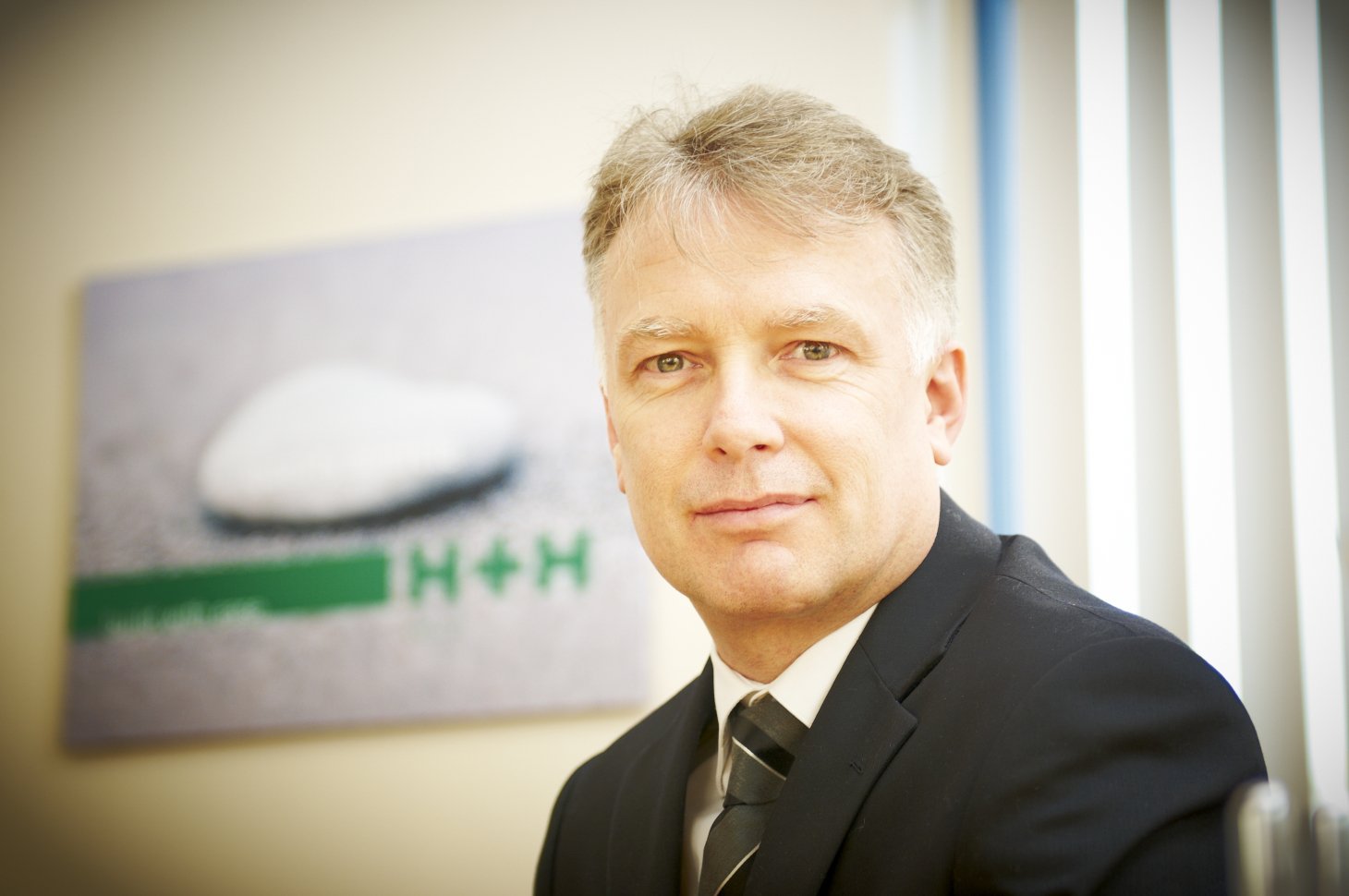
Neil Thomas, Director of Housing at H+H considers the current drive to MMC
So MMC is the solution for the housing crisis? As a shorthand for the need to reinvigorate the housebuilding industry to deliver higher volumes fast, it’s as good a term as any other.
But there lies the problem – the term MMC is too often used interchangeably with “offsite” or “modular build”. To confuse these terms entirely misconstrues the point of the drive towards the adoption of MMCs.
Listening to some commentators (many of whom really should know better) you would be forgiven for thinking that government is committed to ensuring all new houses are built entirely in a factory and delivered, fully complete, to site.
Certainly, a lot of government money, through schemes such as the Affordable Homes programme, require recipients to demonstrate a commitment to Modern Methods of Construction. But if anyone thinks this inevitably involves the immediate creation of a raft of housebuilding factories, they are mistaken.
The current working definition of MMC – put together by Mark Farmer – tackles the issue in the right order. Focusing on the desired outcome: more, high-quality homes built using less people, his stepped approach defines seven categories of MMC, recognising that innovation comes in many forms and that change will be incremental.
This seems both pragmatic and forward-thinking. Encouraging innovation without imposing any pre-conceived vision of what that innovation should look like.
In my view, this approach cries out for collaboration. With a collaborative approach to problem-solving we can move the agenda forward.
There is no shortage of innovative products and ideas in the housebuilding industry; we just need to find the solutions that work best for everyone. A result that is most likely to come from trusted partners working together.
Working for the UK’s largest provider of aircrete blocks, I am not infrequently asked if my products are simply anachronistic in the current MMC-focused market?
Obviously the answer is no – but it is a more complicated answer than simply to point out that our Standard Grade aircrete blocks are still the most in-demand product.
H+H has a range of solutions that tick the MMC box, from Thin-Joint through to Celcon Elements used in the I-House system build. Getting these solutions widely accepted is down to working in partnership with our housebuilding customers, developing the right solutions, at the right time to suit their business models.
MMC products have been used in Europe for years, but there is never any gain from trying to impose a solution – the market has to be ready for it.
Is the market ready now? I think we have reached a tipping point. High demand coinciding with a reduction in the workforce is a perfect storm that none of us can ignore.
What I am absolutely sure of is that housebuilders will find their own solutions, probably from within their existing supply chains. If we start from the objective: more high-quality homes, and work collaboratively, there is a whole realm of innovation waiting to be unlocked.