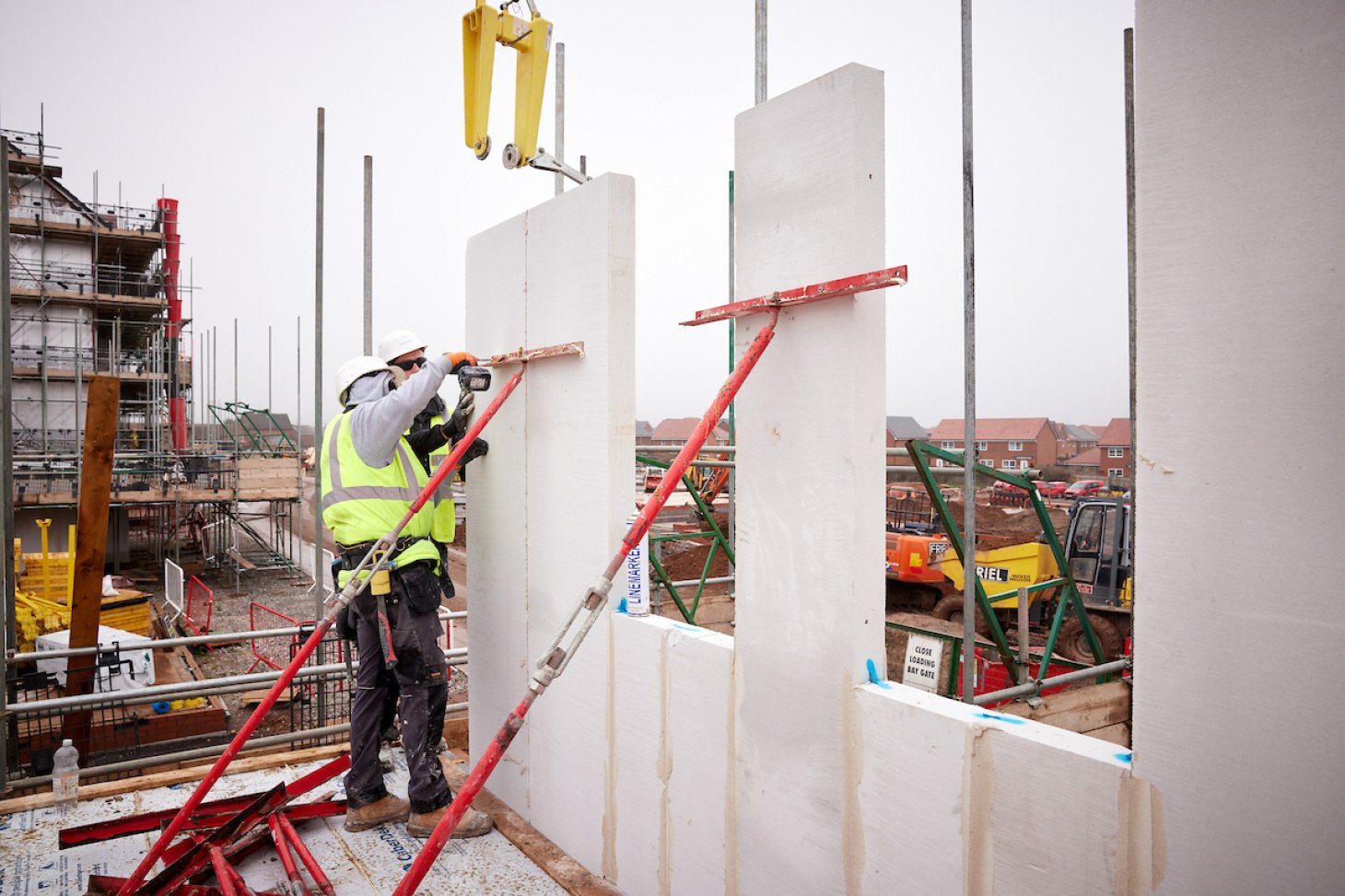
In the 2019 Conservative Party manifesto, the government committed to supporting modern methods of construction (MMC) as part of its goal to construct 300,000 homes annually by the mid-2020s. This included a plan to subsidise modular building. The decision to subsidise modular house building was influenced by a report by Mark Farmer, the government's champion for MMC. Farmer's report, positioning itself as a blueprint for a housing-led industrial strategy, recommended the construction of 75,000 modular homes annually.
However, just four years later, concerns arose that the government was failing to achieve its target with several modular manufacturers facing financial difficulties, others going into administration or ceasing production. In response to these challenges, the House of Lords Built Environment Committee initiated an inquiry titled 'MMC – what's gone wrong?' to investigate the obstacles hindering the increased delivery of MMC homes.
What has gone wrong?
A key finding of the inquiry has shown that Housing Associations are paying more for modular homes than for traditional projects. Giving evidence to the inquiry, Katie Gilmartin of Platform Housing Group revealed that Platform is not commissioning Category 1 modular homes, as the costs are not “workable”, costing up to 50% more than traditional projects.
Beyond the evident cost issues, exemplified by the collapse of numerous modular companies, the practical and environmental concerns regarding modular construction are noteworthy. With sustainability becoming an increasing point of focus in the construction industry, concerns arise over the environmental impact of modular homes, in particular their limited life span compared to masonry-built homes. Traditional masonry constructions, whether using traditional blockwork or modern methods of construction, have a life expectancy of over 150 years, while contemporary modular homes in the UK are designed to last only 60 years. Is it environmentally, or indeed financially, viable to be building homes that may need to be demolished in just 60 years? With 35 and 40 year mortgages becoming more common surely homes should be designed to endure beyond a single mortgage term?
Transporting modules to construction sites via lorries poses further environmental and safety concerns, as well as practical difficulties. During transportation, effective weather coverage of these large modules is challenging, often leaving them exposed to the elements throughout the journey. On-site, these modules may remain exposed until the entire building achieves weatherproofing, increasing the risk of moisture exposure. This exposure poses health and safety concerns related to dampness and mould. Just last year, L&G modular homes encountered issues with mould in homes under construction in Bristol and North Yorkshire.
Building standards for modular homes, particularly regarding fire safety, have also raised concern. In December 2022, the National Fire Chiefs Council expressed 'significant uncertainty' about the fire performance of modular homes, emphasising the need for stricter testing protocols.
What is next for MMC?
The government’s subsidisation of MMC is finite, Housing Minister Lee Rowley has cautioned that the government ‘can’t subsidise forever.’ Considering the multifaceted challenges to modular building, it is only right to begin to question the construction of homes with a limited lifespan and the potential health and safety risks inherent in the modular building process. This prompts a crucial question: are there established and proven modern methods of construction that warrant the government's attention?
Indeed, there exist validated MMC solutions currently deployed with success. Should the government encourage the adoption of such methods for private housebuilding and social housing? H+H Vertical Wall Panels, for instance, which offer notable advantages. These storey-height panels of aircrete are used to form the inner leaf of external walls. Panels are craned into place onto standard foundations and installed using H+H VWP mortar – fast-setting and very strong. The use of Vertical Wall Panels offers a rapid build speed and proven durability.
The solution
In an evidence session for the House of Lords inquiry into MMC, Edward Jezeph from Homes England outlined 15 key performance indicators against which MMC homes are measured. These included pace and cost of build, labour productivity, planning issues, safety, energy efficiency, and sales performance.
Against this backdrop, H+H's Vertical Wall Panels emerge as a comprehensive solution, easily meeting the established performance metrics for MMC homes. The lightweight panels are readily available, offer a rapid build speed and are cost-effective. The cellular structure of aircrete gives the blocks exceptional thermal efficiency and using aircrete can greatly enhance the energy performance of a building’s structural fabric. Fire and moisture resistant, aircrete blocks also provide incredibly high levels of safety. All of this underscores the compelling case for the adoption of H+H’s Vertical Wall Panels in the context of modern construction practices.
Award-winning development company Galion Ltd recently used H+H’s Vertical Wall Panels for the build of five large homes in Somerset. Tim Barnes, Managing Director of Galion Ltd shared his perspective on the use of the panels: “I’m struggling to see a downside to the system. Everyone who has seen it has been impressed and I think once other companies see contractors building with it, they’ll wonder why they’re not using it too. We’re already planning to use the system at another site that will be breaking ground soon.”
In the ever-evolving landscape of construction practices, H+H's Vertical Wall Panels represent a tried and tested, fast-paced and cost-effective method of building homes with exceptional thermal efficiency and longevity.