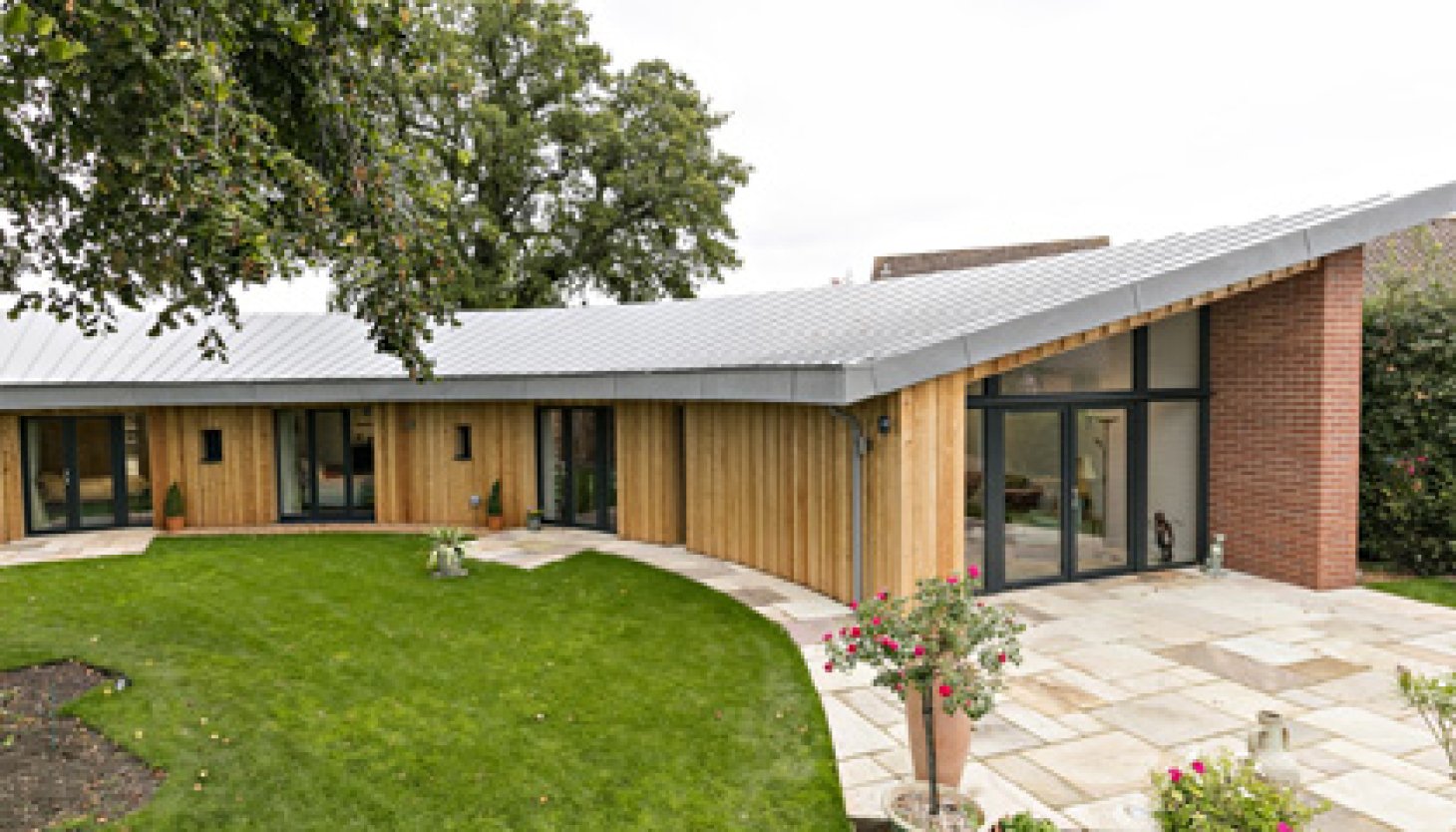
“We were very impressed when we visited one of England’s first Passivhaus homes in Denby Dale and this confirmed our view that we would aim for a fully certified Passivhaus,” say Mr and Mrs Young.
The Youngs are talking about the inspiration for their new, super-low energy custom-built home in Swaffham, Norfolk, which has been built in the garden of their existing house which dates from the early Victorian era and contains several large rooms with high ceilings and fine sash windows. “Although it was a beautiful home with an elegant garden it was increasingly costly to run and maintain. After retirement we felt the need to plan for the future in a smaller and more efficient home,” they explain.
Designed by Parsons + Whittley Architects, their new home was been designed to meet Passivhaus standards which means that it is so well insulated that it needs virtually no heating.“The Passivhaus concept seemed to meet our needs in terms of a flexible build with extremely high energy efficiency,” the Youngs say.
The architect designed the couple’s new single-storey home to curve around a giant Lime Tree which dominates the site. Set beneath its curved, mono-pitched zinc-roof the two-bedroom bungalow features a combination of timber- and brick-faced cavity walls and highly energy efficient triple glazed windows and doors.
To achieve the high levels of thermal performance necessary to meet Passivhaus standards, the inner leaf of the building’s brick-faced cavity walls are constructed using H+H’s 140mm deep aircrete blocks with the 300mm wide cavity between the inner and outer leaf filled with expanded polystyrene (EPS) beads to give a U-value of 0.098W/m2K. The timber faced external walls feature H+H’s 140mm deep aircrete blocks on both internal and external walls; again these are set either side of a 300mm wide cavity filled with EPS beads. This wall with its aircrete inner and outer leafs is even more thermally efficient with a U-value of just 0.096W/m2K.
Using H+H’s aircrete blocks for the external wall’s inner leaf was also beneficial in providing thermal mass to help keep the temperatures stable inside the building. Thermal mass can help maintain a comfortable environment by absorbing heat during the day to help keep spaces cool, it then gives out this heat at night when the temperature drops.
Architect Dan Higginbotham was worked with H+H to develop the walls energy efficient construction. He said: “H+H provided us with advice on block types and their suitability for this Passivhaus project. Compared to a timber frame solution the H+H products allowed for a faster build process, enhanced stability and better thermal mass allowing us to reach Passivhaus standards. This was also the preferred building material for contractor Grocott and Murfit”.
Building contractor Grocott and Murfit Ltd was keen to use H+H’s products having had a positive experience with them on previous projects. The close dimensional tolerance provided by H+H’s aircrete ensured the blocks would fit snuggly together to create a building envelope sufficiently airtight to meet rigorous Passivhaus standards. Aircrete also has exceptional sustainability credentials being manufactured from up to 80% recycled materials.
The bungalow’s construction took 28 weeks, with the inner aircrete shell going up in just three weeks.
“We think that sustainability is a key issue for the country and we feel pleased that our home contributes to a sustainable programme. However, we were primarily driven by the desire to reduce our own energy consumption,” say the Youngs. “We have downsized, but with the slopes and curves in every room we are very comfortable and content”.