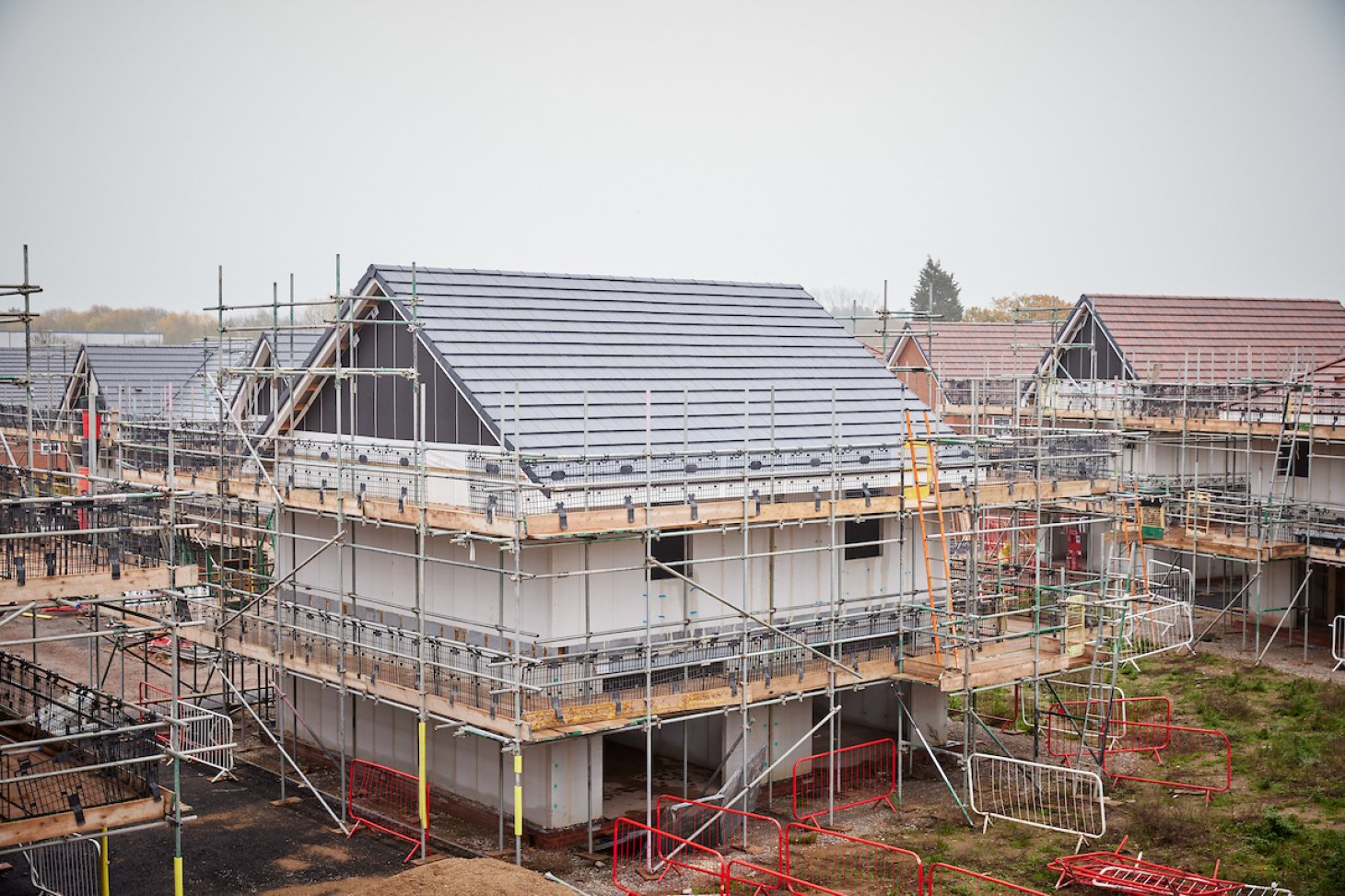
John Churchett, Director of Building Solutions at H+H considers technical innovation in a slower market.
A downside of the over-stretched housing market is its primary emphasis on rapid delivery. The post-pandemic surge in the market has highlighted the strain this puts on manufacturers and builders alike. As these pressures begin to wane, it might be time to revisit the enduring challenges of constructing top-quality homes with fewer hands and increased efficacy.
At H+H, we've always been somewhat sceptical of governmental interference in how the nation’s houses are built – we believe that such choices should rest with organisations specialising in economically feasible home delivery. The private market is known for its unpredictability, and our housebuilders have developed a business model that equips them to weather significant demand shifts.
This volatility works absolutely against the model of volumetric modular assembly. Housebuilding “factories” require massive investment to start and then rely on consistent demand to keep solvent. Despite constant government pressure, and public money, the factory construction model is once again proving fallible.
Behind these headline schemes, however, is a steady development of innovative building solutions that meet the requirement for modern building methods without challenging successful business models and without completely rethinking the building process.
Innovation is always welcome, but the term “MMC” has never been prescriptive. When Mark Farmer was commissioned to define MMC, he identified a range of potential solutions with the emphasis very much on results rather than methods. If a new method or product helps to meet the objective of delivering higher quality homes to more consistent standards, then it can be defined as an MMC.
An example of such an innovation would be H+H Vertical Wall Panels. Storey-high aircrete panels, VWPs can be used as an element within a complete fabric solution or used by the housebuilder as a fast way to deliver thermally efficient walls with fewer people.
We have demonstrated time and again that aircrete can provide homes to meet the most exacting thermal requirements of successive building standards. Most recently, H+H is involved in Project 80: a collaboration between Midlands Heart housing association and Birmingham City University.
In this project, a series of homes have been developed to meet the Future Homes Standard, with post-construction performance being closely monitored to understand the experience of building occupants living with a range of renewable technology. The first phase of the project was based on masonry construction with aircrete used in the majority of the homes and easily meeting the fabric performance standards required by the FHS.
We continually seek to collaborate with our housebuilder partners to innovate using aircrete – a reliable and efficient material known for its thermal performance and airtightness. If the present calmer market affords more room for exploration and advanced technical progress, then it might pave the way for superior home quality in the future.