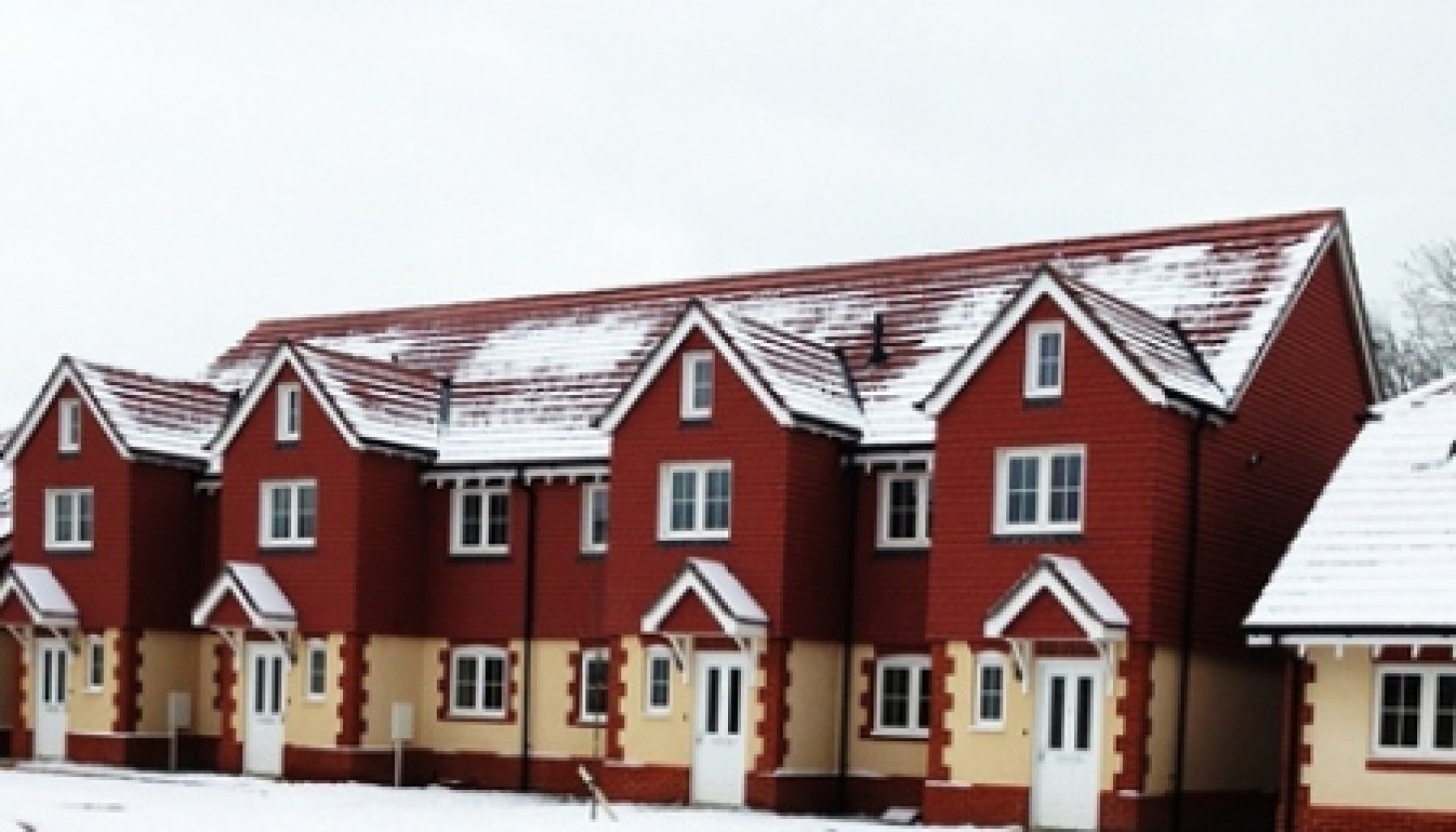
H+H’s Multi-Plate Package has been used to build six houses, as part of a social housing project, in Seaford, Sussex.
H+H Multi Plates are a new generation of aircrete products which are 2½ times the size of a traditional concrete block meaning they can significantly increase build speed.
Multi-plates are sold exclusively as part of a package which includes all the materials required to build structural walls.
Production Director Eddie Owen, of Owen’s Brickwork, highlights this as a key reason to choose the package system: “It encompasses all issues in one system, reducing the stress on our buyer. It’s more viable, financially and practically.”
The six-unit scheme, by developers Trinity Homes, had to comply with Level 4 of the Code for Sustainable Homes. A 25% reduction in CO2 emissions, when compared to Building Regulations (2010), is required to meet Level 4.
This was an important consideration for the contractor, Owen says: “For a project such as this, Code Level 4 social units, our options were timber frame or thin-joint blockwork. Our track record with H+H meant we were more than happy to go down the thin-joint road.”
As part of the Multi-Plate package H+H can link buyers with contractors trained in installing the Multi-Plate package system. Owen’s Brickwork are one such trained company who had previously worked closely with Trinity Homes on other projects.
This is the third time that Trinity Homes has employed the Multi-Plate Package for its property developments, which span Sussex, Surrey and Kent. Neil Bacon, Procurement Manager for Trinity Homes, says: “We like the Multi-Plate package for many reasons but particularly for speed.”
H+H Multi-Plates are made to extremely tight manufacturing dimensional tolerances, and are supplied specifically for use with a 2mm joint of Celfix thin-layer mortar. This allows for little or no levelling, further enhancing the time-saving benefits of the Package System.
The project was completed at the end of 2012.