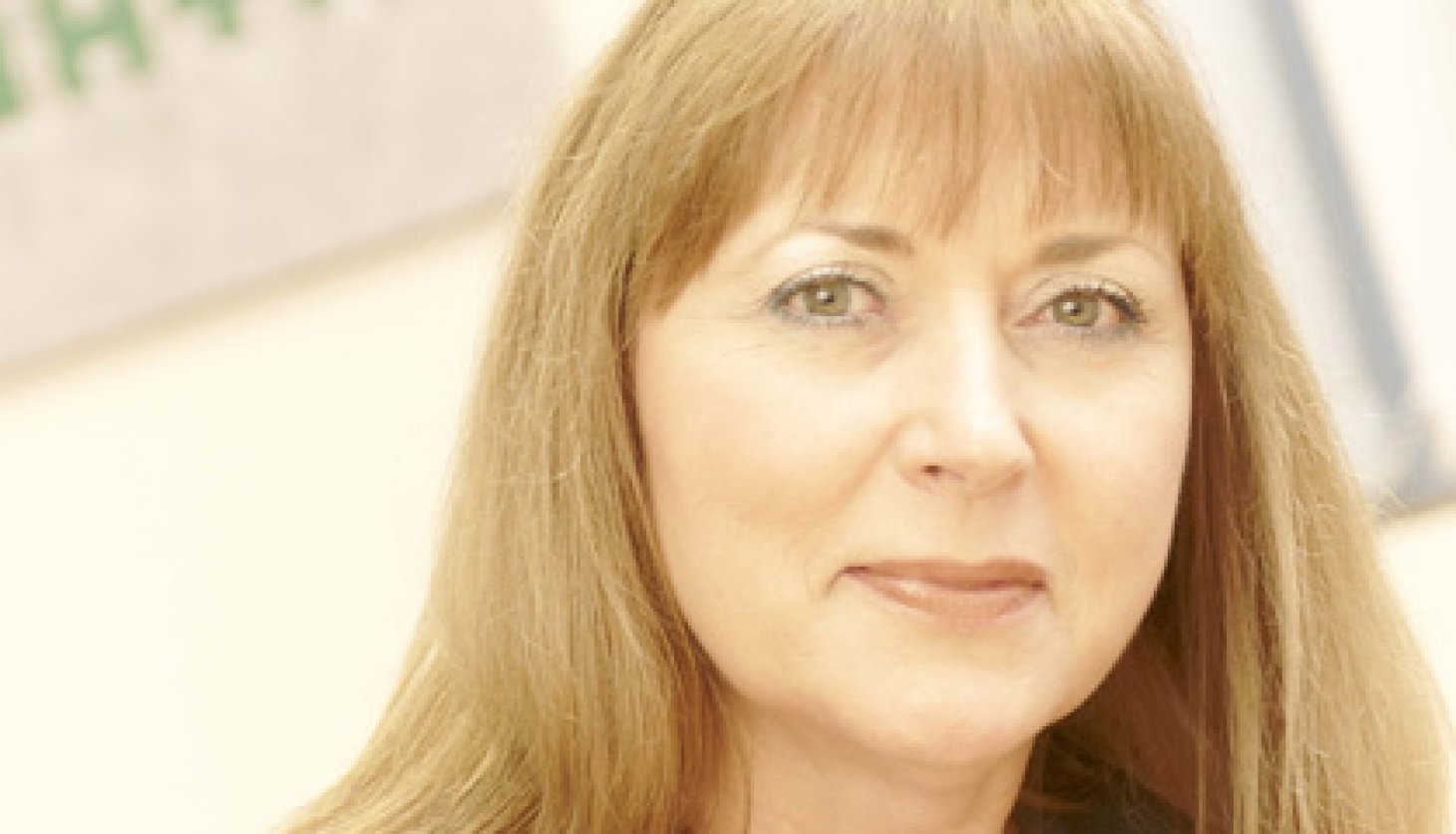
How do the products contribute to the sustainability agenda, and what are their sustainability credentials?
As a material aircrete ticks many of the sustainability boxes. At least 70% of every H+H aircrete block is made of pulverised fuel ash – a waste material that is a by-product of energy generation that would otherwise go to landfill. As a result, our constructions achieve very high ratings in the BRE’s Green Guide.
We also score highly on any rating that looks at the issue of local sourcing. Manufactured entirely in the UK from locally sourced material, our products do not accumulate significant “air miles” in travel and also contribute to employment and wealth around our manufacturing bases.
H+H has also focused close attention on the energy efficiency of our production processes. We were the first aircrete manufacturer to be awarded the Carbon Trust Standard, and the first company to be awarded a ‘very good’ rating in BES 6001:2008 Standard for the Responsible Sourcing of Construction Products.
Just as significant is the role our products play in the construction of sustainable buildings. Our philosophy is very much one of “fabric first” – that energy efficiency should be built into the fabric of a house so that it remains effective for the lifetime of the building. We believe that this is a far better option than relying on technologies that are either unproven over the longer term or rely on the behaviour of the building occupants for their effect.
What is the firm doing in terms of producing Robust Details to assist specifiers and grow its market share in the UK?
As would be expected of a quality manufacturer, H+H supports its products with a range of technical documents, standard specification drawings, performance calculations and Robust Details – all of which are available from our website. All technical guidance documents are naturally updated as regulations or site practice change with the most recent robust details focusing on the area of separating walls. Our website contains a comprehensive range of technical guidance documents while our technical team is also available to answer specific queries.
How does aircrete get those air bubbles?
During manufacturing pulverised fuel ash is mixed with cement and aluminium oxide. A chemical reaction causes air bubbles to be formed in the mixture which rises and increases in volume (a bit like a cake mixture). This texture is then solidified during the autoclaving (high pressure steam) process, ensuring the blocks are filled with small air pockets. It is this structure that gives aircrete its characteristic light weight and thermal insulation.
Can I cut aircrete?
The product’s flexibility in use is one of its most attractive characteristics. The light weight helps with manual handling regulations on site while the blocks can be cut accurately with a saw to accommodate the need for individual sizes and shapes.
What about strength?
Aircrete blocks are available in different strengths. H+H's aircrete products are available in Solar Grade at 2.9N/mm2 and Standard Grade at 3.6N/mm2. H+H High Strength Grade and Super Strength Grade provide compressive strengths of 7.3N/mm2 and 8.7N/mm2 respectively and are designed for uses where higher compressive strengths are required such as in the foundations and lower storeys of three storey buildings, piers under high vertical loads and in multi-storey buildings.
What is H+H?
H+H is a Danish company that manufacturers aircrete in 10 European countries. In the UK the most widely recognised product name is Celcon. Our Celcon Blocks are our biggest selling products.
Where are the blocks made?
H+H operates two manufacturing sites – Borough Green in Kent and Pollington in Yorkshire. Products are delivered either to merchants for stock or direct to site throughout the UK.