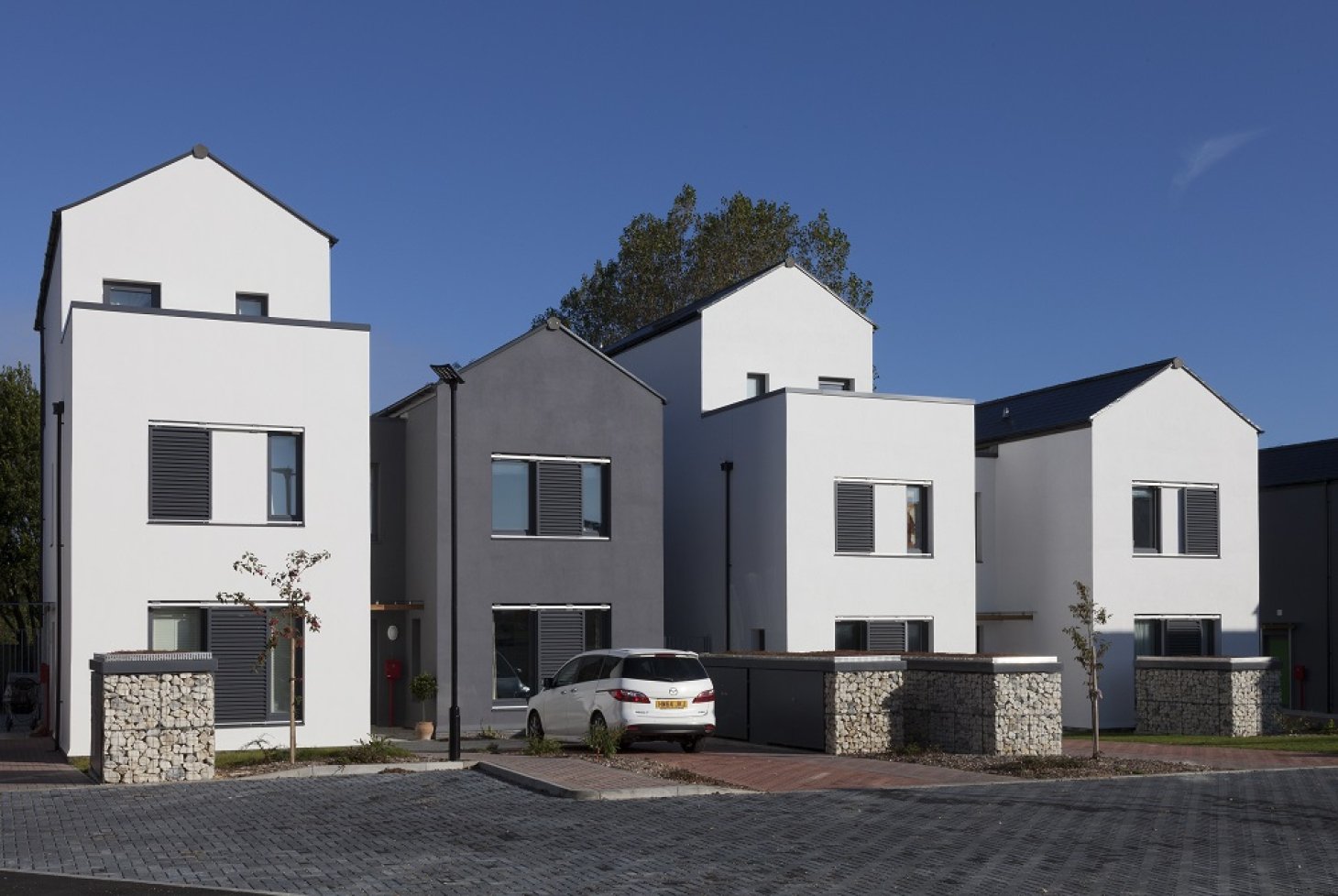
With Passivhaus building methods growing in popularity, aircrete can be a first-choice material for airtight walls.
Soaring energy costs are certainly focusing attention on the immediate impact of inefficient housing and Passivhaus building methods are gaining popularity.
It is estimated that there are around 1,500 certified Passivhaus homes in the UK with many more being built to the standard but not officially certified.
The building method is one way to make new homes zero energy in use. Technically challenging, the building process needs to be accurate, high quality and thoroughly tested. With very high levels of thermal insulation the structure also needs to be airtight. The Passivhaus Standard requires a maximum of 0.6 air changes per hour at 50 Pascals pressure, and every building needs to be tested individually to gain certification.
H+H, with its belief in a “fabric first” approach to energy efficiency, has always supported Passivhaus principles and our aircrete blocks have been used in a number of projects that demonstrate how the principles can work.
The Cameron Close development in the Isle of Wight is one of the most significant. The project was commissioned by Southern Housing Group which was looking for a way to reduce energy bills for its tenants. The Trust did not set out specifically to demonstrate an innovative building method – in reality, Passivhaus was a pragmatic solution to the need for lower living costs.
The design combines 16 semi-detached houses and 12 sheltered accommodation apartments. Passivhaus consultant WARM was involved at every stage of the process including post-occupancy evaluation. This latter stage is what marks the scheme out as exceptional. Airtight wall construction
To get the thermal and air tightness performance required, PCKO Architects opted for a solid wall construction using Thin-Joint blockwork from H+H.
Contractor Stoneham Construction was new to Thin-Joint but took to the meticulous building method easily, noting that it was around 20% faster than traditional blockwork. David Harris, Director of Stoneham is a supporter of the method:
“Passivhaus is all about air tightness so if you can reduce the gap between blocks to 2mm instead of 10mm it makes life a lot easier.”
Building the homes was only the first part of this remarkable project. WARM consultants were retained to carry out a two-year post occupancy study of the performance of the homes.
Comfortable living
Lower electricity bills than the national average were a good starting point, but gas bills were markedly lower, with many residents reporting that they simply did not use their heating at all. Residents all reported satisfaction with lower energy bills.
Just as importantly, the residents were comfortable and happy with the indoor temperatures all year round. The study particularly looked for any sign of overheating as this can be a problem for highly insulated airtight homes. This project, however, had considered the potential for overheating at the design stage and the orientation of the buildings, together with an external shutter system and through-ventilation avoided summer heat spikes.60% reduction in CO2 emissions.
WARM consultants went on to calculate the overall CO2 emissions from all energy consumption and compared it with national benchmarks and targets. The average CO2 emissions for Cameron Close were 60% lower than the average of UK households at the time.
This project demonstrates how Thin-Joint aircrete can contribute to highly efficient housing with minimal CO2 emissions. Another example of a familiar material being used for modern building solutions.