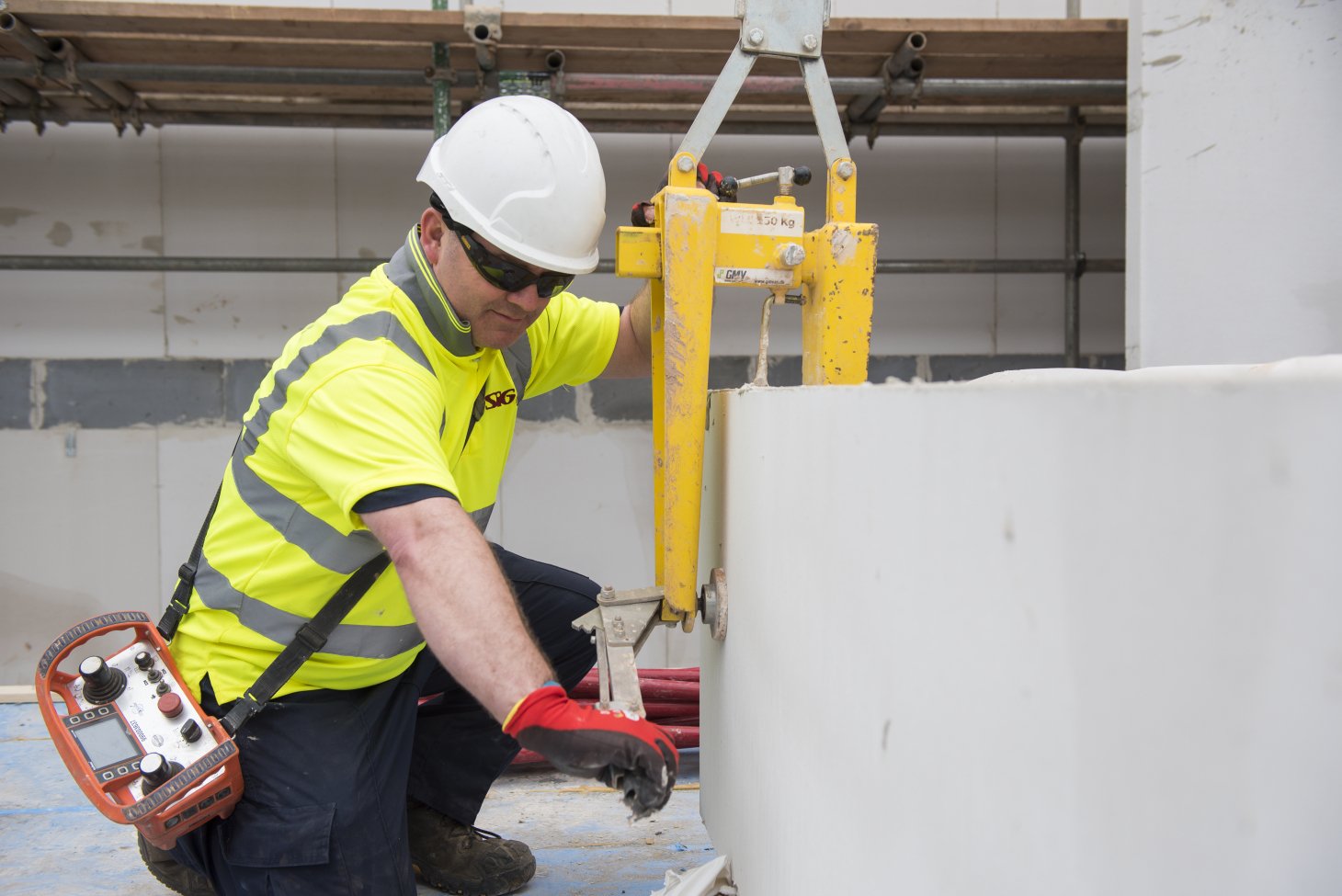
Delivering those 300,000 homes per year is a challenge and attention is very focused right now on Modern Methods of Construction. But what does MMC actually mean?
It’s an important question as much government money (for example, through the Homes Building Fund or Affordable Homes Programme) is aimed at encouraging the development of MMC solutions.
Which is all fine as long as we are clear about what is an MMC solution.
The MHCLG has commissioned Mark Farmer (as in, Modernise or Die) to look at the issue and suggest some ways of dealing with what is becoming a politically charged terminology.
Very sensibly, his report focuses on the desired outcome: more high-quality new homes, faster, and includes a range of approaches to reach that objective.
It suggests seven categories of MMC, from improvements in site practice at level seven to full-scale modular construction at level one.
By using a stepped approach, this encourages all organisations to identify ways to improve their current building practice and to “move up” the levels in time.
So far, so good. As aircrete manufacturers, we are very comfortable with this as a number of our technical solutions will fit happily within the “seven stages” of MMC, allowing developers to take advantage of time and labour savings while also retaining the robust, durable performance advantages of aircrete.
Second on the agenda is acceptance. As Kit Malthouse pointed out in a recent talk at Housing 2019, we have been here before in terms of developing offsite solutions, and the industry – just as importantly, the mortgage and finance industry that supports it - is nervous. Nervous of using new methods without guarantees of durability and robust warranties.
Where warranties are concerned, we need robust warranties that certify the whole building, not just the individual elements from which they are constructed, and we need a minimum life expectancy.
The Build Offsite Property Assurance Scheme (BOPAS), designed to deal specifically with non-traditional buildings, produces a certification that includes a 60-year design life expectation. Our own I-House solution was one of the first to achieve this accreditation and NHBC warranties are likely to follow suit.
And one further issue is the lifetime performance of MMC buildings. What happens in twenty years’ time when a homeowner wants to convert their loft or extend their kitchen? Who will know what the structural design of the property is or what alterations it is likely to be able to withstand?
Aircrete houses, with significant structural strength and well-understood performance, are ripe for this type of alteration. And they need to be – according to research by Savills the average house buyer will now live in their home for 23 years.
The proposed solution is a central register, a database of how all housing stock is built, linked to standard definitions and certification status. This logical solution does pose some pretty big questions, however. Such as who is going to collect, store and pay for this data? And who is going to persuade the builders to share their intellectual property?
Aside from these practical considerations, it is hard to ignore the need to embrace new methods and at H+H we’re well up for that.
Aircrete as a material may not have changed much in the 50 years since it was developed, but methods of building with it have definitely moved on. We would be delighted to see our Thin-Joint and Celcon Elements adopted more widely and are pleased to see a growing UK interest in these modern building methods – already tried, tested and trusted across Europe.
Does aircrete have a future? You bet it does. A long, long future.