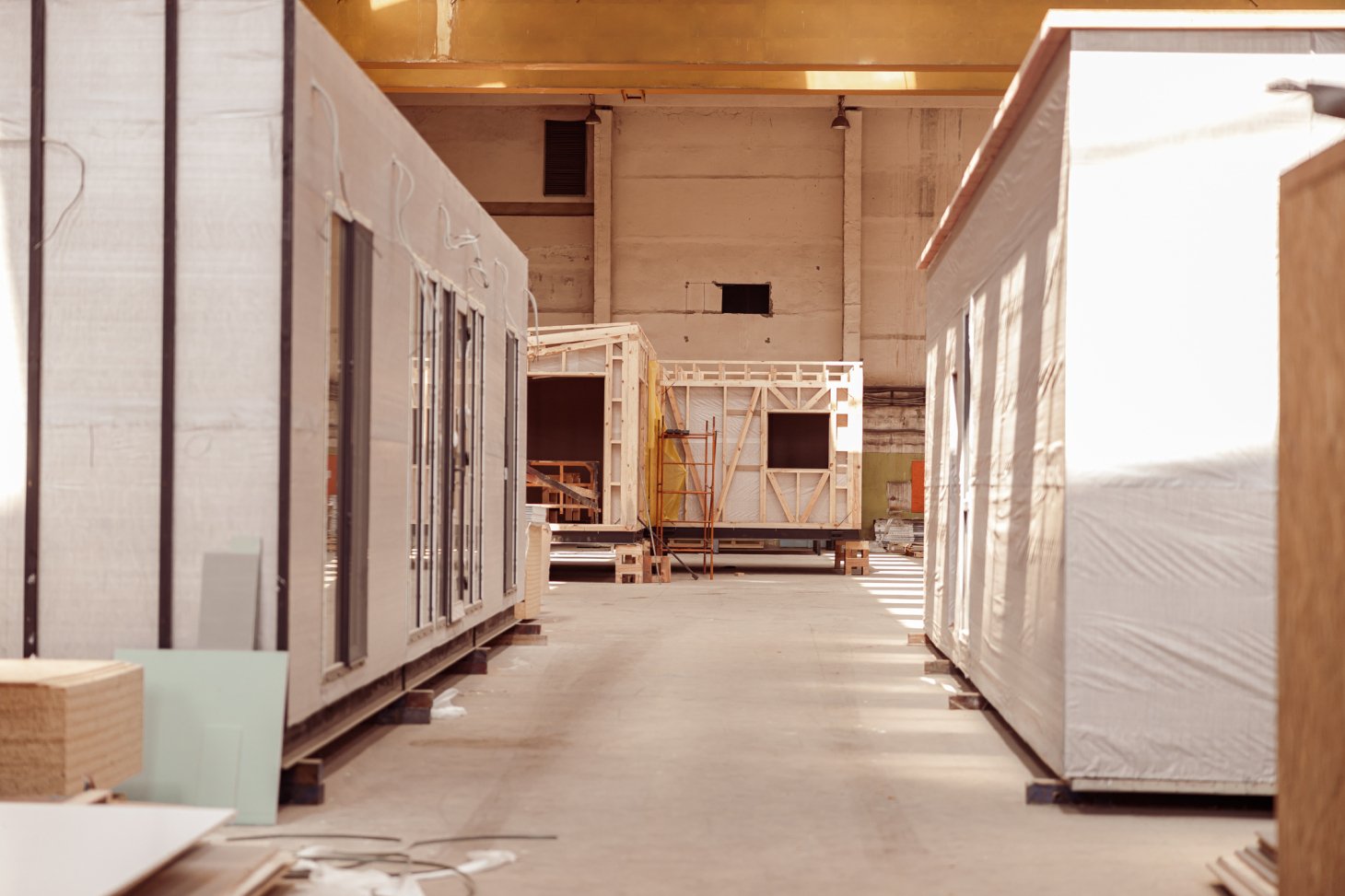
Offsite pioneer Modulous became the latest casualty of the current swathe of modular building company bankruptcies. This, despite the fact that Modulous, describing itself as a “kit of parts”, had none of the pricey infrastructure of factories that weighed down other volumetric companies such as Ilke Homes and Beattie Passive.
Pioneers and market disrupters are always risky ventures but the following points are particularly relevant in this instance:
1. There is nothing new in the idea of factory-built homes. And nothing new in the litany of failure of such enterprises.
2. Volumetric, factory assembled structures do not suit the economic model, the logistical challenges or the skills base of the UK housebuilding sector.
3. Constantly chasing the ideal of precise, factory-built home units results in repeated losses for investors. When those investors include the Government, taxpayers should be asking questions.
As long ago as 1926, architectural pioneer Walter Gropius speculated on a future where lower-cost housing would be made possible by “the manufacture by mass production methods of stock dwellings which are no longer constructed at the site but are produced in special factories”.
It’s a seductive vision. Muddy building sites replaced by clean, productive factories building homes with precision in quality-controlled settings. Repeated government-backed attempts to kick-start a modular construction industry looks to the mass production of vehicles as a model – but is that analogy convincing?
There are numerous problems with the factory-built homes vision of MMC, but let’s just focus on one – the financial model.
Factory-built homes need factories. Factories involve huge investment and require a reliable and consistent market for their products. UK housebuilding, with its near total reliance on consumer confidence, has simply never provided that degree of consistency.
In its review of the modular housing sector “Modern Methods of Construction – what’s gone wrong?” the Built Environment Select Committee looked for answers from, among others, Homes England which was keen to defend its significant investment in modular factory companies. The conclusion of this scrutiny was summarised in January this year by Chair Lord Moylan: “The Government needs to change tack. Simply throwing money at the sector hasn’t worked.” Quite.
A problem of presentation?
Part of the problem is with the presentation of MMC as a concept. Modern does not necessarily equate to pre-assembled and Method does not necessarily mean factory-based house units. The accepted definition of MMC (following on from the Farmer Report) is based around seven categories and only Category One requires the use of factory-built entities.
As Lord Moylan indicates, government funding whose objective is to deliver a greater volume of high-quality homes, needs better targeting, informed by a much deeper understanding of the structure of the UK housebuilding sector. Surely the Government’s role should be to stimulate the market and invest in new social housing, but be less enthusiastic in trying to dictate how new homes should be delivered.
H+H has always supported innovative approaches to house construction – our own Vertical Wall Panels and i-House System represent a strong commitment to new concepts and radical ideas. The difference is that these initiatives are evolutionary, rather than revolutionary.
The Built Environment Select Committee acknowledged the success of much Category Two MMC innovation (where our Vertical Wall Panel solution fits), and of the remaining five categories. That recognition absolutely supports the principle of evolutionary change.
Rather than going through another expensive loop of financial support for a delivery model that has proven so problematic, we would strongly advocate for a government that takes the time to really understand the housebuilding supply chain; focuses on creating an economic environment in which housebuilding can grow to meet demand; and leave the mechanics to the industry itself.