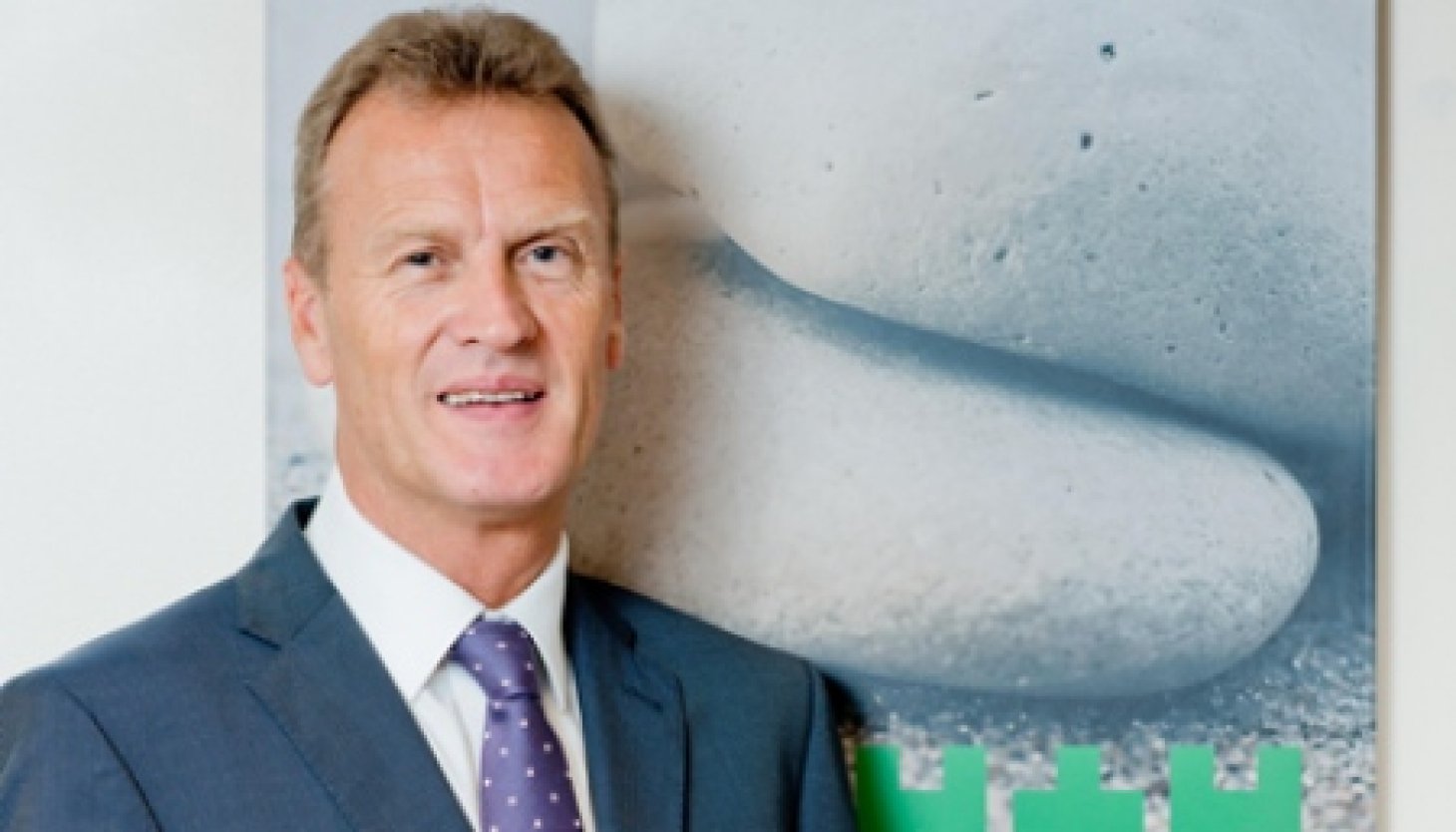
Cliff Fudge, Technical Director at H+H, looks at the popularity of masonry construction and analyses it in relation to the recently announced Part L Building Regulations changes and the potential issue of overheating.
In April some of the most far reaching changes to the energy regulations will come into effect. Part L of the Building Regulations deals with the conservation of fuel and power. The changes have been introduced to help the government meet its commitment to reduce the UK’s greenhouse gas emissions by 80% by 2050. To comply with the new rules buildings will need to be better insulated and have improved airtightness.
Under the changes new homes will have to reduce carbon emissions by 6%. For non-domestic buildings the requirements are even more onerous with a requirement for a 9% reduction in carbon emissions. The new rules will apply to planning applications submitted after the 6th April. Guidance on meeting the changes to Part L is detailed in the accompanying Approved Document L.
The changes apply to new buildings. There are no changes to the regulation governing works to existing homes and non-domestic buildings.
Similarly, there are no changes to the limiting fabric U-values, which are the maximum allowable U-value for building elements. For walls the U-value remains at 0.3W/m2K; although in practice it is likely this value will need to be lower in order to meet other requirements (the lower the U-value of a building’s fabric these less energy is required to maintain comfortable conditions inside the building).
For new domestic buildings the revisions to Part L introduce a new fabric energy efficiency rate (FEE). This has been introduced to close the current loophole that allows the use of renewable and low-carbon technologies to be used to offset a comparatively poor fabric performance. As a result, the changes to the regulations now put the focus firmly on achieving a good thermal performance for the building’s fabric.
Adopting a fabric-first approach makes a lot of sense. It is far more cost effective to focus on a building’s fabric at the outset rather than trying to improve thermal efficiency later in a building’s life. This approach also has the advantage of providing a permanent, energy efficient solution that will be in place for the lifetime of the building, as opposed to the alternative of achieving compliance using more short-lived, and often inefficient, renewable technologies such as solar electric (photovoltaic) panels.
These changes come about as the popularity of masonry construction, one of only a small number of building methods to have survived through the times regardless of new technologies, is on the increase.
NHBC’s Housing Market Report published in January this year revealed that 13 per cent of new homes registered in the UK in 2013 where built from timber frame. This leads one to believe that around 84-87 per cent were built using masonry, an increase of around 2 per cent since 2012 and approximately 10 per cent since 2009.
When it comes to achieving the fabric-first solution endorsed in the new Part L for a new dwelling, one of the most beneficial components of a masonry wall construction is aircrete. Aircrete has the advantage of having an inherent thermal efficiency, which helps in the drive to minimise fabric U-values with improved thermal bridging details and reduce the demand for heat energy in winter.
Aircrete, combined with thin-joint mortar, also helps reduce the air permeability of a wall, decreasing the amount of heat lost through air infiltration. What’s more, when aircrete is used as part of a thin-joint solution it has the additional benefit of speeding up construction by enabling the inner leaf of a cavity wall to be constructed independently of the outer leaf.
The benefits of aircrete are not simply confined to helping keep homes warm in winter; aircrete’s high thermal mass also helps in keeping buildings cool in summer.
One of the consequences of the government’s drive to improve the fabric energy efficiency is that it can sometimes lead to lightweight buildings overheating in summer. This is because a highly insulated fabric is advantageous when it comes to homes retaining heat in winter. It is, however, less beneficial on a warm summer’s day, particularly once the heat from occupants, large numbers of electrical appliances, and solar gains is included.
As a result of these heat gains, new homes that are constructed from lightweight materials are becoming increasingly hot. This can be extremely uncomfortable for the occupants and, can increase the risk of respiratory and cardiovascular disease.
The advantage of an aircrete construction is that it has a relatively high thermal mass, which allows the walls to absorb and release heat. Aircrete is particularly effective when used for the construction of the inner leaf of a cavity wall where it has been left exposed or it is given a wet plaster finish.
Thermal mass has a big advantage of allowing the walls to absorb heat during the day, which helps limit the rise in internal temperature. The heat is stored until internal temperatures fall, when the heat is released back into the building. The cycle repeats on the next day.
The challenge with this solution is that for thermal mass to work as an effective solution to overheating, it is usually necessary to flush away the released-heat at night by opening the windows to encourage ventilation. This solution works well in the UK, where night-time temperatures are lower than the day-time peak.
The recent spate of extreme wet and windy weather helps illustrate how unpredictable the weather in the UK can be. Longer term the weather is even more difficult to forecast. What is certain is that the weather is changing so that we can expect more and more outbreaks of extreme weather. The advantage of an aircrete solution is that it will provides a thermally efficient, long-term solution that will comply with Part L that is sufficiently robust to ensure occupiers can remain comfortable in temperature extremes.