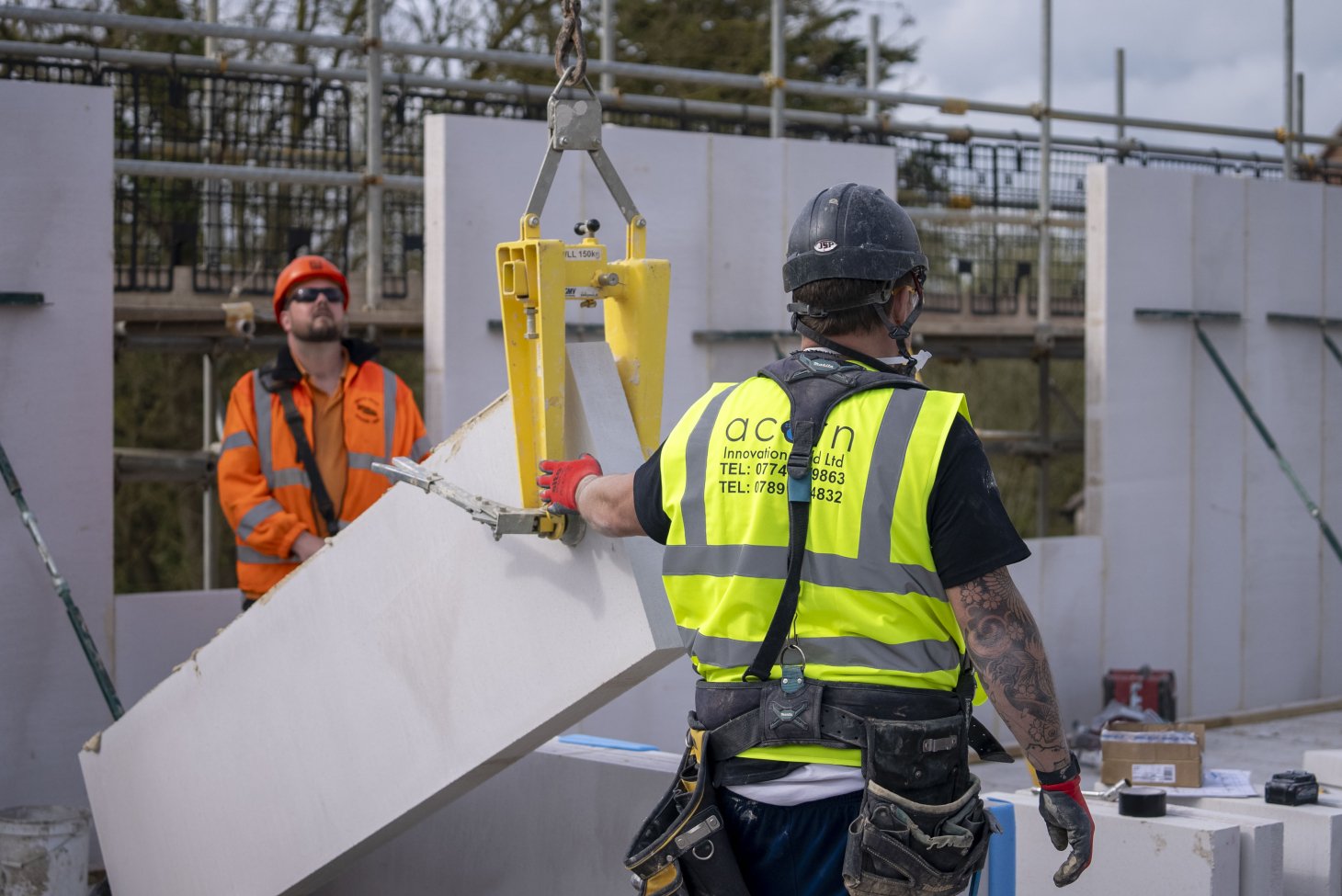
Modern Methods of Construction or MMC are building processes that aim to make construction faster and more efficient than using traditional techniques. They often include some element of offsite construction. Modern Methods of Construction range from ‘modular construction’, where whole units are manufactured in a factory and delivered to site on the back of a lorry, to traditional building products that have been modified to require less labour on site.
What are the benefits of MMC?
The housebuilding industry is currently dealing with a perfect storm of issues: an ambitious housebuilding target set by the government to alleviate the housing crisis, combined with an acute labour shortage and a growing skills gap. The benefit of Modern Methods of Construction is that they can provide a more efficient way of building.
The main benefits of Modern Methods of Construction (MMC) are:
• Speed of build
• Fewer workers required on site
• Reduced waste
• Improved quality control
• Predictability of build
If used effectively MMC can deliver a faster build while requiring less labour, without compromising on the quality of the finished homes.
What’s the history of MMC?
The first real appearance of Modern Methods of Construction in the UK came after the Second World War to address a severe housing shortage. Prefabricated houses were made in factories and speedily erected as part of the “Homes Fit for Heroes” initiative, providing a quick, affordable solution to meet the huge demand for new homes.
Although intended as a temporary fix, many of these homes are still standing today. Designed to last just 10 years, they have often been lived in for decades, leading to widespread issues as materials degraded. This has left the term ‘prefabricated’ - or ‘prefab’ – with negative connotations, often associated with damp, unhealthy living conditions.
How is MMC used in construction today?
The quality of MMC systems has advanced dramatically since the post-war era. Today, with the UK in the midst of a ‘housing crisis’, there is growing demand for fast, affordable housing. MMC returned to the spotlight in 2016 with Mark Farmer’s Modernise or Die report, the outcome of an independent review into the construction industry’s labour model, commissioned by the government.
Farmer’s report identified key failings in the UK construction industry and urged it to embrace new working practices. He championed Modern Methods of Construction as a key driver to increasing housing delivery despite the looming labour shortage.
What types of MMC are there?
Following Mark Farmer’s report, the government launched a task force which developed a new categorised definition framework for different forms of innovative construction methodologies.
There isn’t a single answer to the question: what are modern methods of construction? In fact, there are 7 MMC categories:
• Category 1 – Pre-Manufacturing - 3D primary structural systems
• Category 2 – Pre-Manufacturing - 2D primary structural systems
• Category 3 – Pre-Manufacturing - Non systemised structural components
• Category 4 – Pre-Manufacturing - Additive Manufacturing
• Category 5 – Pre-Manufacturing – Non-structural assemblies and sub-assemblies
• Category 6 – Traditional building product led site labour reduction/productivity improvements
• Category 7 – Site process led labour reduction/productivity improvements
This is worth noting as there is a common misconception that Modern Methods of Construction and modular construction are the same thing. In reality, modular construction - also known as ‘volumetric modular construction’ - is just one type of MMC, falling under Category 1.
It is important to realise the distinction, particularly as modular construction has faced some widely publicised challenges in the UK over the last few years. These issues have resulted in many companies, some with government funding, going out of business, raising questions as to whether modular construction is the right fit for the UK housebuilding industry.
Does H+H offer any MMC solutions?
H+H manufactures Vertical Wall Panels which are MMC Categories 2, 3 and 6 compliant. Vertical Wall Panels (VWPs) are storey-height panels of aircrete which are craned into place onto standard foundations and can build a house shell from DPC to roof in just five days.
When used as part of a housebuilding package, with prefabricated timber floors and roofing system, VWPs offer a Category 2 MMC solution.
VWPs offer a fast build masonry alternative to timber frame MMC systems, offering all the benefits that come with using a tried and tested masonry material in addition to the construction advantages of an MMC solution. EPDs are available for Celcon Vertical Wall Panels.
Homes built with aircrete offer many benefits including excellent fire resistance, excellent thermal properties and acoustic insulation, resistance to damp and mould, and robustness for a long lasting build.
Modern Methods of Construction have come a long way since the post-war prefabs, offering a smarter, faster way to build. With proven solutions like H+H’s Vertical Wall Panels, MMC is helping to meet today’s housing challenges without compromising on quality or durability.