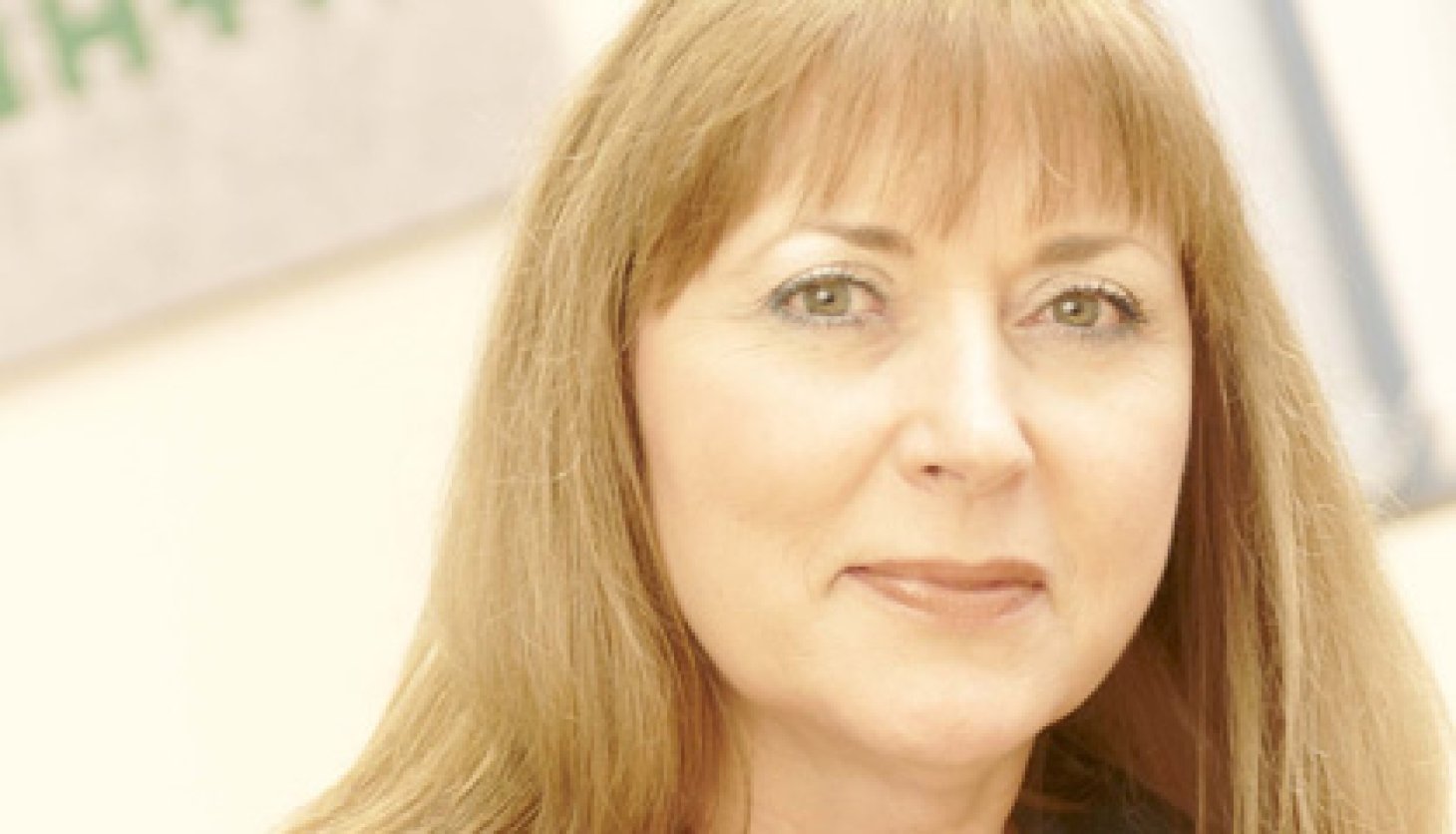
The recent upheaval surrounding the Government’s Feed in Tariff for small scale renewable energy generation has added uncertainty into this marketplace. Is it now as appealing for housing associations to install potentially expensive technology, such as solar PV, on new builds, as it was just one year ago? Perhaps not, and testament to this are the number of micro generation schemes either shelved or put up for review recently by HA’s.
A further worry for the sector is the new multi-installation tariff rate, which is 20% less than the new standard rate, as is the need for properties to meet a minimum requirement for energy efficiency to qualify for standard FIT payments.
According to DECC , under this requirement, PV installations post April 1st 2012 will only be eligible for standard FIT tariffs if they can provide a valid Energy Performance Certificate (EPC) at the time of application for FITs, showing a rating of level D or above for the property to which the solar panels are attached or wired to provide electricity.
Installations that do not meet the requirement will receive a lower tariff of 9p/kWh, a nominal amount at best. This means getting the building fabric as thermally efficient and airtight as possible is vitally important, in both new build and existing buildings.
Binding targets exist to reduce the nation’s carbon emissions and housing represents a significant proportion of these. New housing in particular must be built to energy efficient levels and to do so without using renewable technology represents a conundrum that needs resolving. To do so cost effectively is even more of a challenge, especially bearing in mind the current environment.
One way to go about this is to use a ‘fabric first’ methodology. Bearing in mind that a building envelope will last for many decades and renewable technology less so, it would make sense to get the building fabric to work as well as possible first, maximising air tightness and reducing heat loss through the structure.
Many solar PV systems only have guaranteed power output for 25 years, so over a building’s lifetime, they may need to be replaced or upgraded many times. In some extreme cases, solar PV systems have even been blown off roofs and they can also cause roofs to leak. This phenomenon was highlighted last year by the NHBC. It found increased installations of solar PV systems on roofs have led to more roofs leaking.
Furthermore, renewable technologies such as wind and solar require some form of understanding from whoever ends up living in the house as well as possible maintenance and repair.
Contrast that with the building envelope, which once built should stay weather-tight and maintenance free for years with little input required from a tenant.
Built correctly, a ‘future proofed’ fabric should also not need expensive and potentially tricky refurbishment in future, as much of our existing housing stock currently requires. Aircrete constructions, being masonry, are incredibly robust and therefore offer all these advantages and more.
Aircrete blocks are themselves inherently highly insulating and made from mostly recycled content. Completed aircrete shells also offer some thermal mass (to help regulate the temperature in hot weather) over and above standard timber frame options.
Of course, to build to high levels of the CFSH using a fabric first approach is not easy and doing so whilst minimising costs is harder still. It is widely recognised that a method of building high code compliant homes that are both cost-effective must be found.
H+H has been actively involved with the Technology Strategy Board project, AIMC4, looking at exactly how to volume build to Code level 4 cost-effectively using a fabric first solution. The initial findings of this were recently announced and it is clear that methods already exist to build to Code level 4 without using renewables, including using aircrete and thin joint technologies.
However, challenges remain, especially with regard to getting all elements of the supply chain to work more closely cutting down on time, waste and therefore cost.
An excellent solution to better supply chain integration that has come out of the AIMC4 project are ‘sandpit’ days where all the supply chain partners get together in a form of brainstorm sessions. These sessions occurred more than once to discuss how best all the products involved could fit best together.
H+H worked particularly closely with Solar Windows of Caerphilly to decide how best our blocks and windows could fit together in the pursuit of airtightness and thermal efficiency. For a fabric first approach to work there must be perfect integration between all elements of building envelope and this collaboration of supply partners makes this possible.
An example of a recent housing project built using aircrete with thin joint mortar, to level 4 of the CFSH with no renewable technologies, is at the Stondonfield social housing scheme in Essex.
This made use of aircrete High Strength 7.3N/mm2 Jumbo Bloks for the external walls, Standard Grade 3.6/mm2 Jumbo Bloks for the partitions (fixed with thin-joint Celfix mortar) and Standard Grade Celcon Foundation Blocks. The external walls at this project provide average U-values of 0.14W/m2K, well within both FEES and Zero carbon Hub Specification C standards.